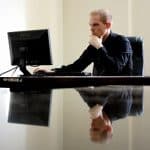
A topic that often comes up lately is high turnover, especially the perception that this is common and desirable among millennials. Born in the mid eighties, I am right on the cusp between millennial and Generation X, and I am one of the aforementioned employees with a high turnover history. A specialized Reliability Engineer with nearly ten years of work experience, I have rarely stayed with a company much over two years. I never intended to be a person who moved between companies so regularly, it just kind of happened.
Here are some symptoms of the problem, or reasons why employees like me might leave:
- Higher pay far beyond the typical 3% annual wage increase;
- Increased likelihood of getting a promotion to a higher pay grade;
- Unsatisfying company culture;
- Lack of challenging work;
- Company does not value or invest in professional development;
- Better work-life balance;
- Changes in their family situation;
- Improved benefits.
If you look at the data, there is a single root cause why skilled employees like me come and go: companies don’t make it worth it to stay. I’m not really sure why this is, because it is so expensive to replace outgoing employees with special skill sets like Reliability.
For example:
Outgoing Employee Costs
An outgoing employee will cost you extra money. Time spent on administrative costs like exit interviews by HR and payroll changes might be around $1,000 . Then you have to pay them unused vacation, which might total about 2 weeks pay (~$8,000). Estimated outgoing employee cost would then be about $9,000.
Incoming Employee Costs
Typical costs for hiring a new employee might include things like administrative costs, recruiter fees, training, and the cost to pay an employee during their initial training phase. This adds up quickly. Let’s assume for this thought experiment you are trying to replace a $100,000 salaried engineer.
Administrative costs might cover the overhead for an HR employee to perform the work (5 hrs X $50/hr = $250), the cost of travel for the interview itself ($2,000), and the time spent by several interviewers (5 hrs X $75/hr = $375). Also, you must include the costs of a drug test and background check, estimated cost of $2,000. Total administrative costs of $4,625.
Recruiter fees for a $100,000 employee might be around $30,000.
Sign on bonus and relocation estimated at $50,000.
Training costs might be about $5,000 in the first year. This would include internal training, and at least one off-site technical course to get them up to speed. You might also want to add in a conference, so people in your industry can get to know the new engineer, so add another $4,000 just to be sure. Total for training would then be about $9,000.
Training time opportunity loss would be at least four weeks of time that the new employee is not useful. This is pretty conservative; a lot of estimates would put this at as much as a year. Using salary alone and not added benefits, this cost would be approximately $8,500. I’ll round it up to an even $10,000 to include some of the company’s benefit costs.
This brings our total out to:
Outgoing Employee + Admin Costs + Recruiter Fees + Sign On and Relo + Training + Training Time = Total Cost of New Employee
$9,000 + $4,625 + $30,000 + $50,000 + $9,000 + $10,000 = $112,625
All of this leads up to one final truth: you are losing money if you aren’t retaining employees. A lot of money. The costs are quite high. The reasons employees might leave are numerous, and it would be overwhelming to try to address them all.
Just for fun, let’s look at the typical cost to train a new Reliability Engineer. I’m going to estimate about five years to get really good, plus all the training.
Five Years Of Salary: $65,000 + $66,950 + $68,958 + $71,027 + $73,158 = $345,000
Just kidding, these salaries are WAY too low. By five years, a skilled Reliability Engineer should be making more like $85,000. This is a good example of why you are not retaining your Reliability Engineers at a 3% annual raise.
Let’s try that again. To achieve $85,000 by year five, you would need to account for a 7% salary increase per year:
Five Years of Salary: $65,000 + $69,550 + $74,416 + $79,628 + $85,202 = $373,798
Your newly minted Reliability Engineer will also need a lot of training to get to the right level. By year five, a Rotating Equipment Reliability Engineer would be expected to be at least an ISO Cat II Vibration Analyst, Level II Machinery Lubrication and Online Monitoring Training. You should also plan for at least one conference per year.
Vibration Training + Lubrication Training + Online Monitoring Training + Five Years of Conferences = $$$
($1,700 + $350 + $1,900 + $400) + ($1,300 + $1,300) + ($2,300) + ($10,000) = $19,250
So, to summarize, if you can hire a new graduate and spend five years training them as a Rotating Equipment Reliability Engineer, you will end up investing around $400,000 in them. That’s no small change.
Instead of contributing to the churn and wasting money training employees for your competitors, look at the root cause of why employees are leaving: It’s because companies don’t make it worth their while to stay. So instead of trying to address each individual cause, you can either improve your exit interview process to determine which are the biggest factors and address them one-by-one, or develop a unique package that makes a company special enough that employees want to stay.
Some Things That Can Be Done To Better Retain Reliability Engineers:
- Improve engagement to make their activities valued;
- Provide challenging and rewarding work activities;
- Keep abreast of company culture (and act like you care);
- Provide financial or professional development incentives for employees to stay longer than two years;
- Be up-to-date on competitive salaries and benefits;
- Give management support and resources to Reliability activities;
- Don’t ask for absurd amounts of unpaid overtime, focus on the quality of work performed and not the quantity of hours an engineer spends on site;
- Show appreciation by acknowledgement and feedback.
Do you have any ideas or experience with how to retain skilled technical employees? Please share them below!
So true.
I can’t wait to leave my present employer. There is no understanding of reliability or predictive maintenance, only complaints about engineering costs to maintain the programs. All training has been squashed. Professional certification is discouraged.
I took over some programs about 1.5 years ago. In the beginning, the testing efficiency was 10%. Now it is close to 90%. More equipment has been caught, before it ran to failure, than in the last 20 years.
I’ve educated people about what I do but the higher levels of management want to shut my programs down. The ignorance is depressing. On top of that, I’m working through a severe , painful physical handicap, so it is no fun being here.
In general, Ann Arbor is very parochial, backward and has a run-to-failure culture. The Troy area in Michgan is a better area for reliability professionals.
No one should stay in one place if they are wasting their time (I’ve been here 13 years).
You will never master the craft if you don’t move around. I’ve learned the hard way that specific regions of the U.S. are more receptive to reliability principles than other regions. Millennials, you have the right idea..
I really love what you said about ways to retain reliability engineers, like improving your engagement to make their activities valued. My husband works with many engineers and wants to have a good relationship with them so they are more likely to want to work with him. Thank you for the ideas about making sure you provide them with challenging and rewarding work activities as well not asking for absurd amounts of unpaid overtime.