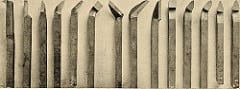
Reliability is about making the right decision, each time.
Answering Questions
A common role during a first assignment as a reliability engineering is to answer a question or accomplish a task. It may help someone to make reliability decisions.
We may be asked, as I was, how long will this new product function during use? The director of engineering wanted to know if the new design was reliable enough to meet the customer’s requirements concerning reliability. He didn’t ask it that way, yet he did have a question that needed answering.
Sometimes we run a batch of tests, conduct failure analysis on field returns, or compare the durability to two vendor subsystems. In each case, there is a question to be answered.
A decision to be made by someone else.
Enabling Decisions
Our teams make decision day in and day out. They include considering cost, time to market, functionality, and sometimes, reliability. It is our role to make considering the decisions impact on reliability easy. To be part of everyone’s decision making process, they need the right information to enable them to fully consider, tradeoff, balance, and eventually decide.
First, do you and your entire team know the cost of a failure? How much does it cost the organization when a product fails for a customer?
Not the overall warranty costs or accruals, instead
- the cost of call center support,
- shipping a new unit out,
- shipping the failed unit back,
- the cost of the replacement unit,
- the cost of diagnostics and repair.
If known, what is the cost of lost sales due to dissatisfied customers.
In general, this cost of a failure is two and one half times the retail price. If you have nothing else, use that to get started.
The cost of failure allows someone, anyone, to convert a change in failure rate along with expected shipping volume to quickly calculate the cost or benefit of a change in a failure rate. A one percent improvement in failure rate may sound nice and something we should do. When the benefit of reducing the failure rate one percent is $1.25 million for a $10k cost, then it’s obvious.
Second, follow the money. Determine and understand what is the underlying motivation of the key decision makers. What drives their decisions as it often guides the decisions of a large portion of the organization, as well.
For example, I once worked in a group where the procurement team earned a nice bonus if they were able to cut purchase cost of the components for our product by 10%. Unfortunately, they did not count the cost of field failures as part of the cost calculations.
On more than one occasion, a small, insignificant, no one will notice, change to a slightly less expensive part, with the same form, fit, and function, resulted in a significant increase in field failures. On the other hand, using a slightly more robust and expensive part would reduce field failures.
Gather the evidence and help your major decision makers change the calculations of ‘cost savings’ to include the costs of field failures.
Third, provide guidelines and training. A Design for Reliability guideline that includes key tools including:
- FMEA
- HALT
- ALT
- Reliability Statistics
- Derating
- Safety factors
The idea is to provide the necessary information and framework for decision making.
Another element for guidelines and training is an internal system for lessons learned. How do you avoid making future mistakes, how to keep the guidelines updated, etc.
Great Reliability Decision Making
Each decision the includes the full consideration of the impact on reliability performance is a great decision.
The decision to start production knowing the risks, that the risks are acceptable, and knowing there is a high likelihood the product will meet customer reliability expectation is an example. Another is deciding to select one vendor over another, in part based on the two vendor’s reliability maturity.
Every decision can be a great one.
Summary
Reliability engineering do not design or produce products. Thus we do not directly create the eventual reliability performance.
Your role as a reliability engineer is to influence, enable, promote making decision that have all the information necessary related to reliability. Your role is to create a culture where every decision is a great reliability decision.
Leave a Reply