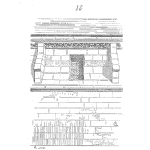
Environmental and Use Manual
How well can you describe the use conditions your product will experience?
How well do you need to know the use conditions?
For some situations, the environment for your product is assessable, others are not. For some situations, we guess the range of expected stresses, others we measure.
The design process and the myriad decisions that impact product reliability rely on characterized environmental stresses.
A great place to consolidate how and where customers will use your product (including the relevant stress factors) is in an environmental manual.
A ground benign Army Private
Out of high school, I joined the US Army. I was a private in an artillery battalion. Not being aware of the military specifications of ‘ground being’ we just worked and practiced in the heart of Texas (Fort Hood to be precise).
It snowed gently, rained hard, and got blistering hot and humid. Our equipment had to work.
Most of the time though, it was pretty nice. Light winds, calm days, and pleasant temperatures. Our equipment had to work.
Later in my military career (all during peacetime) I was stationed in Germany and spent many, many weeks training at Grafenwöhr. Here it got cold, hot, dusty, and often rather nice.
One winter exercise the heater in my vehicle (an armored, tracked, metal box of a vehicle) failed. Overnight the breath of 5 sleeping soldiers froze the inside roof an inch thick. We were lucky it didn’t fall on our heads during the night. Our radios and other gear experienced a similar environmental stress.
Nearby a tracked howitzer (looks like a tank with very large bore cannon attached) wouldn’t start in the cold. The soldiers built a fire under the crankcase to warm the engine and oil.
It worked and the massive diesel engine started about 30 minutes later.
I’ve looked and have never seen a military specification for ice build up inside a vehicle or fire exposure for engines.
You may have to live with your product and customers to fully understand the range and types of stresses your product will experience.
Testing is not how a customer uses your product
Your set of environmental tests, waterfall testing, or stress testing routine is now how your product experiences the world.
Customers press buttons with fingernails, pens, and sometimes with the fleshy part of there finger — gently. Customers press buttons at nearly any angle they can. The idea for each stress that is relevant to failure mechanisms likely to occur is to characterize
- how often,
- what angle,
- under what conditions,
- and with what force,
They will press the button, for example.
The same process applies to any stress. Min and max temperatures are not sufficient. How often at each temperature is necessary information to inform design decisions that impact reliability.
Pressing a button a million time using a test jig is not representative of how the button exists. A button that is rarely used yet exposed to sunscreen and dust may fail after only 3 cycles due to excessive contamination and build up of gunk.
The test conditions are not the environment. Your understanding of the environment and use patterns should both inform your team’s design decisions, and for the areas of high risk of failure, inform your environmental testing.
Create a useful environmental description and test
An environmental manual may start with minimums, nominal, and maximums for the set of expected stresses that may lead to product failure.
Quickly move on to gathering the rest of the data.
For salient failure mechanisms, determine the relevant stresses. For those stresses characterize the environment or use conditions. Get enough data to create histograms or distributions.
Get the data to allow the design team and your future environmental testing to assess materials, different use patterns, different sets of environmental conditions, and allow detailed physics of failure modeling.
Focus on stresses that impact failure mechanisms.
Different types of customers
Not all customers are the same. Not all customers live in the same environment.
Some press buttons with the end of a ballpoint pen often, while others only use their fingernails. Some live in salt fog filled coastal villages with poor electrical power quality, while others live inland near a quarry (dust and vibration).
How many use the product often or very little? How many live near the coast or city or in the various different environments that exist on the planet?
For inkjet printers, the team had five different types of users. Plus, we knew more than 70% lived within 50 miles of an ocean coast.
We ran experiments and measured transportation vibration and temperature profiles, print frequency profiles, and indoor temperature and humidity profiles.
Knowing the customers, including how and where they used the product matters when creating a product that works for them.
Different environments
The military specifications have a set of environments from ground benign to space. Few create systems that operate across such a range of environments.
At HP we had five defined environments. We included home, outdoor portable, and computer room, for example.
If a new product wasn’t going to be used one of the existing defined environments, we had a framework to gather and organize the necessary data.
Start with the failure mechanisms
I said it before, only gather the data you need. The stresses that affect failure mechanisms are those that matter.
Use the risk assessments you are already doing, including the FMEAs, to identify the likely set of failure mechanisms. Subsequent HALT or any failures for that matter may add to the list of suspect failure mechanisms.
Each failure mechanism may have one or more stresses that influence the occurrence of the failure.
For example, if you know that corrosion is a failure mechanism, then temperature, humidity (possibly), voltage (possibly), abrasion (remove protective coatings over time), etc. Are possible stresses that you will have to characterize.
Include shipping, storage, transportation, and installation.
Summary
Yes, it is a big task.
You will likely never finish the manual. Design teams are clever and often find new materials, structures, and systems. Customers are clever in finding new ways to use (abuse) your product.
Do not stop with a long list of stresses and testing. Provide enough detail for your team to understand the risks, understand the tradeoffs and understand how their decisions impact reliability.
Change in use over the life cycle may also affect failure mechanisms. Conventional thermal power plants experience thermal cycling variation due to market conditions, (fuel costs, dispatch order, on/off due to reliability and human error). Predicting cumulative cycles is an important design requirement.
Very true Gene, I heard that the inclusion of solar power on the grid has set up new cycles that impact the transitional plants adversely. Plenty of changes in any product that need proper care and anticipation by the design team. cheers, Fred