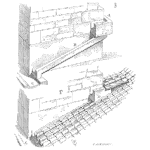
How do you decide what level and type of maintenance to use on an individual item of plant and its sub-assemblies? Not all equipment is equally important to your business. Some are critical to production and without them the process stops. Others are important and will eventually affect production if they cannot be returned to service in time. While other items of plant are not important at all and can fail and not affect production for a very long time.
Keywords: risk-based maintenance, preventative maintenance
As a maintainer and operator, you want to know which equipment in your plant falls into each of those categories so you can determine your response. Furthermore, you want to know which sub-assemblies in each item of equipment are critical to the operation of the machine.
From this information, you can decide which spares to hold on-site and which to leave as outside purchases. The equipment criticality also determines what level of preventative maintenance to use, what type and amount of condition monitoring to use and what type and amount of observation is required from the operators. You can also use it to justify on-line monitoring systems to protect against catastrophic failure.
The two approaches often used to determine criticality is either Reliability Centered Maintenance or Risk-Based Maintenance. Both methods determine the consequences of failure and then address the appropriate response to prevent the failure. One other way of determining equipment criticality is to consider knock-on effect of a failure and the severity of the consequences. It is the same intention as the previously mentioned methods but it arrives at the rating and the response in a quick four-step process.
People from operations and maintenance work through it together, equipment by equipment, using the simple flow chart below. Those failures that cause safety and environmental risks were not allowed to happen and either the parts were carried as spares and changed out before failure or the plant item is put on a condition monitoring program. Those failures that caused production loss or affect quality is also not allowed to happen or put into a condition- monitoring program. And those failures that didn’t matter are treated as a breakdown.
The flowchart (kindly provides by Sumitomo Chemicals of Japan) lets one arrive at a rating and a corrective action for each piece of equipment and component. If an equipment or component loss produces dangerous situations, or if the failure stops production or affects quality, it is either changed out before the end of its working life or put on a monitoring program.
Mike Sondalini – Maintenance Engineer
We (Accendo Reliability) published this article with the kind permission of Feed Forward Publishing, a subsidiary of BIN95.com
Web: trade-school.education
E-mail: info@trade-school.education
If you found this interesting you may like the ebook Process Control Essentials.
Leave a Reply