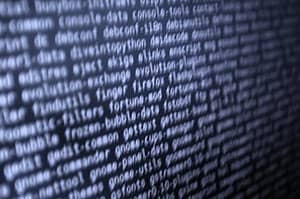
How Capturing the Right Information Will Improve Your Job Plans, Increase Reliability and Improve Your Profitability
One of the most important, but often the least effective parts of the Maintenance Planning & Scheduling process, is the work order close out step. Here critical data is supposed to be captured and used to improve the job plan, identify future work and improve reliability. All of these add up to improve the profitability of the organization.
So why do so many organization fail to capture the data required? Often times it comes down to a few reasons;
- The organization does not know what data should be collected, why it is needed or what to do with it. In a reactive organization, this is often the case as there is no time to utilize the Plan-Do-Check-Act cycle, or even think about it.
- The data process is not well thought out and is too cumbersome to use effectively. Often times organizations use generic failure coding for all equipment. This results in the craft having to sort through hundreds or thousands of codes to find the right one.
- The data may be captured, but is not utilized or results not realized, so the data collection stops. Would you continue to put in the extra time to collect and provide data, only to find it not being used?
I remember working with a maintenance department to start recording the proper data when the craft closed their work order. At the time the craft was only recording the time spent on the work and if it was completed or not. Although it was a start, it was far from desirable. We needed the right data to drive sustainable improvements in the organization. So we started off small; asking the craft to mark up the PM routines with anything that did not apply or needed to be changed. They responded that they use to do that, but nothing was ever updated so why waste their time.
Changing this attitude would not be easy, but if it was, all organizations would have great data to work with. Utilizing their honest and prompt feedback, we began to develop the change program to ensure we would have the right data moving forward.
We started off by defining what data would be mandatory and how it would all be used;
Mandatory Data | How It Would Be Used |
Who worked on the task and the hours spent on the work order | Update job plan estimates, for better scheduling;
Ability to RCA premature failures; |
Parts & Materials Used to Complete the Work Order | Update job plans;
Better forecast part requirements; |
Updates to the Job Plan, which includes any changes to resourcing, procedures, set points, and Tips | Improve job plans for improved effectiveness and efficiency;
Build a knowledge management system; |
Any Issues encountered, that delayed the completion of the job | Improve the Maintenance Process; |
Updates to any drawings
|
Reduces Planning & Troubleshooting Times |
Identification of Follow Up Work
|
Ability to break the reactive cycle |
Failure Coding;
· Failure Mode – Effect by Which the Failure was Observed · Failure Cause – The Circumstances that led to the failure · Component Failed – Specific Part that failed |
Focus on defect elimination, allowing the reactive cycle to be broken |
With the data requirements defined, we had to bring the craft along in the journey and provide us with the data. We relaunched the Work Order Close Out System in a defined process;
- Trained the craft in the what, why, how of the feedback; Multiple sessions were provided on the Planning & Scheduling Process, Data Analysis, and the CMMS
- Communicated the benefits to them of providing feedback; Identified how the craft would specifically benefit from the feedback, such as not looking for parts, reducing the number of times they were pulled from jobs, etc.
- Committed to the craft that the feedback would be used; by signing a declaration and commitment to the timeliness of implementing the feedback.
- Had the craft attempt to break the system; The craft reviewed all of the failure coding, the CMMS, etc. They identified the issues ahead of time so we could address them
- CMMS to Enforce Population of Fields; this ensures that specific fields had to have data in them before the work order could be closed.
- Provided a Standard Text for Non Specific Field Feedback; by providing standard text in the work order, it prompted reminders for the craft to provide the data.
- Maintenance Supervisor Review Close Outs; even with the CMMS enforcing the population of the fields, it does not guarantee that the data is correct. The supervisor would verfity that the data aligns with the job.
- Measured Right First Time Close Out; by measuring and trending how many jobs were closed out right the first time, we were able to identify trouble areas and work to reduce the issues.
- Involving the craft in utilizing the feedback and developing improvements; by involving the craft in the analysis of the data, they could see the data and feedback being utilized. This energized them to provide better feedback.
By defining the requirements, utilizing a change management program, and working with the craft to identify issues and improve them, we were able to successfully capture the mandatory data for over 90% of the work orders within 3 months. A great success, but not without further challenges;
- Computer Access; when this was first rolled out, there were only a few computer workstations available in specific locations. This led to craft waiting to provide the feedback, or not providing the feedback because they had to wait. Additional workstations were added throughout the site, to ensure easy and prompt access. With the additional work stations added, the feedback increased dramatically
- Computer Literacy; some of the older mechanics, were not comfortable with computers, and had no desired to use them. Multiple training courses were provided to all of the maintenance staff to improve computer literacy. The courses ranged from basic computer usage, to Outlook, Word, etc.
- Culture / Attitude; while the change program was designed to address many of the concerns and issues around, this isn’t my job, we still encountered some resistance. We utilized many different approaches to overcome this, from raffles, to coaching, and in rare instances, discipline.
Two years later, the craft continue to provide feedback and the organization has achieved an increase of over 20% uptime and an increase in wrench time of 16%. These improvements would not be possible, without the data to support decision making, and improvements.
What feedback do you capture and what feedback should you be capturing? How will you go about capturing the right data?
Remember, to find success, you must first solve the problem, then achieve the implementation of the solution, and finally sustain winning results.
I’m James Kovacevic
HP RELIABILITY
Solve, Achieve, Sustain
References:
- ADKAR – A Model for Change in Business, Government and Our Community
- Successfully Utilizing CMMS/EAM Systems
Leave a Reply