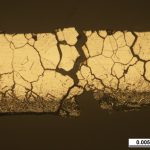
In a previous article I discussed the degradation of materials due to exposure to stressors (use conditions) and how to identify stressors. Cracks form and grow in axles and shafts due to cyclic stress, steel screws corrode when exposed to water, some plastics become brittle when exposed to sunlight, and coatings on surfaces can wear away. When too much degradation occurs, components and joints fail, leading to product failure.
Things to consider during design
If you’re someone who likes to design reliable products, you must think about the stressors and their effects. When designing a product, we must identify the following things
- The stressors that will be acting on the components and joints
- Potential degradation mechanisms
- The amount of degradation that is acceptable
- Whether the degradation will lead to component or joint failure
- The failure mode
This information guides decisions about the mechanical form and materials to use components and joints, the control measures to put in place to ensure that components and joints are fabricated properly, and testing to evaluate product reliability.
I already discussed stressors in a previous article. Two important terms in this list are failure mode and failure mechanism. Understanding their difference and keeping them straight is important.
Failure mechanism
Failure mechanism is the physical process of materials degradation that leads to failure. Here are some examples of failure mechanisms:
- Cracking of a support member exposed to cyclic stress from vibration
- Intergranular corrosion of 304 stainless steel pipe exposed to water
- Crevice corrosion of a bolt and washer exposed to water and road salt
- Fretting wear of a circuit board pad and contact during thermal cycling
- Adhesive wear of two rollers moving against each other
These are just a few of the many different degradation and failure mechanisms. Notice that for corrosion and wear there is more than one degradation mechanism. So, saying that a component will fail by corrosion or wear is not specific enough to understand the actual mechanism and make design decisions to prevent the degradation.
Failure mode
Failure mode is how a component or joint stops functioning. So, for the previous examples we have the following failure modes:
- Fracture
- Leak
- Loss of clamping force
- High electrical resistance
- Change in surface profile
Identifying stressors, failure mode, and failure mechanism
A valuable engineering tool used to identify the information is Failure Modes and Effects Analysis (FMEA). The tool helps focus engineering teams on the factors that influence their products’ reliability and how to address the factors through design decisions, specifications and other control measures, and testing to evaluate reliability.
Using FMEA requires discipline because the process can seem arduous, though it’s really just boring. However, the benefits are tremendous when the efforts result in products that pass reliability testing the first time and field failures don’t occur.
Attend our January 26 workshop to learn about galvanic corrosion and how to design to prevent it.

Leave a Reply