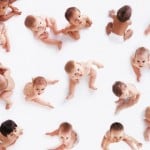
Here is a common situation that is considered when reliability testing is being planned. Let’s use letters to designate depth in a product component structure. The top level product is level “A” and a component in top sub assembly is “B”. A sub assembly, of a sub assembly, of a sub assembly, is at level “D”. So is it more efficient to test the component at level “E” or at level “B”?
Question: Is it more efficient to test the component at level “E” or at level “B” to demonstrate it’s individual goal?
An allocation model is used to derive goals for sub systems based on high-level product goal. It answers the question “If the product reliability goal is 98% what does the reliability of sub assembly XYZ have to be to support the product goal?”
The allocation model has set a goal for assembly XYZ at level “C” at 150,000 hours MTBF. To demonstrate this goal with an 80% confidence it will take 30 units and they will have to be run for six months with no demonstrated failures. The sub assembly at level “B” that it reports to has an MTBF goal of only 15,000 hrs based on the model. This can be demonstrated with four of the “B” units and completed in three months of testing.
But that doesn’t make any sense that you could effectively demonstrate the required confidence in each component at level “C” by running four units of the high-level assembly for three months? Our component that we needed 30 units and six months will not have run the necessary 30 units for six months. We will only have run four of them for three months. Doesn’t sound right???
This works because we are looking to demonstrate probability and express it as a statistical confidence. We have also made a few assumptions. We have assumed that the failures we are pursuing occur randomly. This means that the likelihood of a failure to occur after one hour of use is the same as the likelihood of it occurring at 1,000 hrs of use, as long as we are not n wear-out.
Here is why this works. Let’s imagine we have a baby. We have categorized crying as “failure”, and oh boy is it!. We do what we can to avoid failure, but it happens. At any given time if someone was to walk into the room we estimate there is a 50/50 chance that the baby is crying based on all the random factors that make babies cry. So if you walk into the room once and you do not hear crying you would demonstrate a certain percentage confidence in the goal of 50%. Walk in a second time and hear crying? ok we are on track to demonstrating the failure rate is a true 50%. Walk in 10 times and we got crying six of those times, we can derive a 90% statistical confidence that there is a 50% chance a baby will be crying when you walk in a room.If you walk in If you walk in
Ok but what if we don’t have all day to keep taking samples. Is there a way we could do this quicker? Yes if you can get more babies. If you were able to put 10 babies in a room and then randomly enter the room once you could express a high confidence similar to what was measured with multiple observations. Here is why. Let’s take an extreme to make a point. If each baby has a 50% chance of crying at any point in time and you enter a room with ten babies and no babies are crying it seems very unlikely that the failure rate was a 50% for any individual baby. There is no way 10 babies who each have a 50/50 chance of crying for random reasons are all not crying at the same time. I would say you just demonstrated that the failure rate of these babies is much better than 50/50. So the demonstration of a higher confidence or higher reliability was done with a shorter test at a higher level assembly (a day care).
Which should you do? The test design decision comes down to the logistics of time, money, and space. Is it more cost effective for the program to have a few high-level assemblies run for a shorter time, or many low-level components run for a longer period of time? Just depends on the product we are testing and the program we are in. But the options are there for expressing confidence at as rapid a pace as possible if evaluated in advance.
-Adam
Thanks for this Adam! surely this helps..
may be you can elaborate more on the parametric & non parametric demonstration when the demonstration requirement (MTBF) is too high ?
Sachin,
Could you elaborate on your question a bit further? Are you asking if other factors/variables could be considered to support a higher level demonstration?
Regards,
Adam