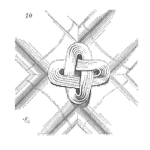
Fibreglass construction and repair. Fibreglass is a glass fibre reinforced plastic composite with excellent chemical resistance properties. Its physical properties, selection of resins and glass, method of construction and fabrication and peculiar repair requirements must be appreciated when using this material.
Keywords: laminate, backing layer, structural layer, corrosion barrier, crack repair, winding angle.
What readers will learn in this article.
- Fibreglass comes in different types and properties.
- Fibreglass construction produces a composite material.
- Fibreglass construction methods and techniques.
- Chemical resistance enhancements.
- Proper methods to repair fibreglass.
Fibreglass is a composite material. Which means it is made of individual constituents combined together into a structure. The key components in fibreglass are the strands of glass fibre and the resin that holds them together. Additives are available for colouring, protection from the sunlight’s ultraviolet rays and to change curing properties.
Several methods are used to make fibreglass items. The most popular being contact moulding by hand, centrifugal casting and filament wound on a mandrel.
MECHANICAL PROPERTIES OF FIBREGLASS
Fibreglass is a brittle, hard material and shatters if hit with a hammer. The resin breaks without warning if overstressed. Fibreglass gets the vast majority of its strength from the glass fibres. The resin takes little load. It only fills the voids between the strands. Tanks, pipes and structures made of fibreglass are built with a large safety factor of 10 to 1.
The glass fibre may be produced from various types of glass. The most common being type ‘E’. The other types of glass are designed to be stronger and tougher.
Several types of resin with varying properties are available. The resins belong to a family of plastics known as thermosets. Once cured they cannot be melted and reformed. They consist of a two-part system – the base and the hardener. When the hardener is stirred into the base, chemical reactions cause the base to harden and set. Those used for acids are vinyl ester based. They soften at about 120o C and are suited for services up to 100o C (212o F).
COMPOSITION AND STRUCTURE OF THE LAMINATE
Chemical plant made from fibreglass is constructed so the cross-section through the laminate (the fibreglass wall) consists of a corrosion barrier, a structural layer and an outer surface layer. Each layer has a specific purpose that in combination give both structural strength and protection from chemical attack. Figure 1 shows the laminate structure through the wall of a tank used for chemical service.
The corrosion barrier is made of two layers – a resin-rich outer layer and a supporting backing layer. The resin-rich layer is 0.25 mm to 0.5 mm (1/64” to 1/32”) thick. A thin surface tissue of type ‘C’ fibreglass mat is imbedded to prevent mixing of the corrosion barrier resin with the fibres in the backing layer just below.
The backing layer is at least 2.5 mm (1/8”) thick and contains type ‘E’ fibreglass making up 20% to 30% of its mass. This is achieved by using glass mat of apt thickness.
Next is a structural layer of ‘E’ glass to carry the loads applied on the material. For contact moulded and centrifugal cast items, chopped or woven mats making up 25% of the mass are used. If filament wound the structural layer must consist of not less than two bi-directional layers of continuous filament. The winding angle for piping and pressure vessels is usually 54o as this gives the best stress distribution ratio between circumferential (hoop) and longitudinal (axial) stresses.
The resin used in the structural layer is not the same as that used in the corrosion barrier. Corrosion barrier resins are expensive and to minimise costs the resin in the structural layer is of a lower chemical resistance.
Outside of the structural layer is the outer surface layer. Its construction depends on whether it is exposed to a chemical or weathering environment. A chemical environment requires a backing layer and a final resin-rich layer as was applied internally. For weathering environments only a resin rich layer and additives to protect against ultraviolet light are needed. Colouring agents are also added to the outer layer.
METHODS OF FABRICATION
The glass fibre is available in several forms. It can be in short chopped strands from 5 mm to 50 mm (1/4” – 2”) made by chopped the glass fibre off a continuous roll. Chopped strand mat is a sheet of short lengths of intertwined cut fibreglass. Rovings are collections of long parallel strands of straight or wound glass fibre that can look like twine or tape. Woven rovings is a sheet made from rovings. Woven cloth is a sheet woven from continuous glass-fibre yarn.
Fabrication can be by contact moulding (also known as hand lay-up) where the resin and glass fibre are placed by hand over a mould. Filament winding is usually used to make tubular shapes like pipes and tanks where rovings are wound onto a mandrel previously prepared by contact moulding. Centrifugal casting is also used to make goods by applying resin and reinforcement to the inside of a rotated mould.
To get consistent strength properties in all directions the glass fibre must be oriented in different directions. This is usually done during the application stage by either selecting glass mat with the strand weave at right-angles or if the item is filament wound by altering the direction of the wound roving in each alternate layer. It is critical that no air voids remain between layers as they create internal stress raisers.
NOZZLE INSTALLATION
Drawing 2 shows one of the two ways nozzles are fitted in fibreglass tanks. The alternative is to continue the nozzle into the tank and put an overlay from the nozzle to the inside wall but that is a poor design for liquid flow. Nozzles less than 50 mm (2”) diameter are gussetted back to the tank.
Note the use a wall reinforcement to stiffen the area of penetration into the tank. The corrosion barrier is reapplied to the end of the nozzle to prevent ‘wicking’ or capillary action drawing chemical into the structural layer of both the nozzle and the tank wall.
REPAIRING FIBREGLASS
Impact damage of fibreglass causes cracking. Cracks can be through the laminate or ‘star’ cracking (crazing) in the outer layers. Abrasion damage can be either a scratch through the corrosion barrier or worn areas where the resin-rich layer has been removed and the structural layer fibres are evident.
Worn area repairs involve roughening the surface and replacing the corrosion barrier and missing structural layer. Star crack repair requires roughening the surface and laying extra structural and corrosive barrier layers overtop. Through-crack repairs require gouging-out the crack and chasing the ends back to undamaged laminate or cutting out the panel containing the crack and replacing it anew.
Cracks, and joint gaps between panels, are filled with resin and glass and a new structural layer and corrosion barrier hand-laid overtop. Before laying new fibreglass prepare the old fibreglass by roughened with a grinding to a minimum distance of 100-mm (4”) either side of the damage. The preparation provides a key between the old and new layers.
Cracks and gaps are filled with resin equal in corrosion resistance to that used in the original manufacture. The first layer of the overlay must straddle the crack by at least 25 mm (1”) either side. Successive layers increase in width and are centered on the crack or join. The outer edges of the overlay taper down to the surface of the laminate to avoid stress concentrations. If possible the repair is done to both surfaces of the laminate.
Mike Sondalini – Maintenance Engineer
We (Accendo Reliability) published this article with the kind permission of Feed Forward Publishing, a subsidiary of BIN95.com
Web: trade-school.education
E-mail: info@trade-school.education
This is a fantastic website with wealth of knowledge on the Fibreglass properties. Keep it up!