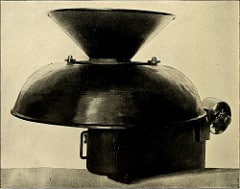
What Does Being In The Flat Part of the Curve Mean?
To mean it means very little, as it rarely occurs. Products fail for a wide range of reasons and each failure follows it’s own path to failure.
As you may understand, some failures tend to occur early, some later. Some we call early life failures, out-of-box failures, etc. Some we deem end of life or wear out failures. There are a few that are truly random in nature, just as a drop or accident causing an overstress fracture, for example.
What we Call the Flat Part of the Curve
Given the classic bathtub curve, the cross-section of a bathtub, with a steeply declining failure rate on one side and a steep rise in failure rate on the other side. The middle is flat and often drawn much as a bathtub with a long flat section between the two bounding curves.
Let’s not consider the failure mechanisms and what causes product failures for a moment. When someone says ‘we are in the flat part’ they are saying we are not enjoying early life failures anymore, and wear out mechanisms haven’t begun as of yet.
It also may imply that we have sorted out the supply chain, assembly, and transportation-related causes of failure such that they have little chance of occurring for customers. And, it may imply that the design, materials, assembly, and understanding of the use conditions suggests that no element of the product should wear out leading to failure for a suitably long time.
From a customer’s perspective, it means there is little chance or an acceptably low chance of failure over the duration of intended use. The relative change in failure rate from one month to the next is small and in many ways could be considered flat.
What Makes Up the Flat Failures
All of the possible ways your product can fail still exist. The chance of an assembly error is very small, yet does exist. The chance of a material or contamination defect leading to rapid wear out is very small, yet does exist.
In fact, for a well designed and assembled product, the chance of any one failure is small, yet something will cause the product to fail eventually. It may be dropped not he loading dock initiating a crack that later leads to an overheating failure. It may operate on a structure with just the wrong natural frequency which excites excessive vibration leading to accelerated solder joint fatigue.
Each individual failure mechanism has it’s own curve and each mechanism either has a decreasing or increasing failure rate. Some units have latent defects which lead to early failures while remaining units do not have similar defects that ever manifest into a failure, thus for the population there is a decreasing failure rate pattern.
Some units have slightly different surface finishes such that the wear rate is slightly higher or lower for individual units, yet all by design wear till deemed a failure. This is characteristic of a wear out failure – the applied stress or use leads to degradation of functional performance for an item till it fails.
It is the mixture of the many failure mechanisms if no one mechanisms dominants the possibilities that creates a low rumble of potential failures. Each is competing to cause a failure. Looking for that opportunity to expose a loss of function. Combining dozen’s if not hundreds of likely yet rare failure mechanisms leads to relatively flat or stead chance of failure.
Here’s the rub. In my experience, there are one or two failure mechanisms that dominate the early failures. A part that has a low Cpk, a design that is not robust to use conditions or very high chance of handling damage. And there typically is one or two mechanisms that dominant the wear out. For industrial electric motors, for example, bearing failures account for 50% or more of all failures.
It is the shape of these dominant failure mechanisms that define the products probability of failure and it’s lack of a flat section. In my experience, it is more like a V than a U. With good design and processes, the V may be rather squat with relatively shallow slopes, yet the flat section is not recognizable.
Achieving a Low Failure Rate Over a Long Duration
Keep in mind that we cannot simply wish or assume to be in the flat part of the curve. It’s not magic and it rarely occurs.
It is the deliberate consideration of the potential failure mechanisms, not the mix. It is the assessment of environmental and use conditions on the materials, design, maintenance, and assembly to understand the long list of potential causes of failure. Then designing and building a product the minimizes the possibilities.
Deliberate, proactive, careful, detailed study, exploration and experimentation leads to a product with a misshapen bathtub with a very shallow or nearly flat chance of failure over an extended duration.
Then a new customer application, a cost reduction, an additional feature comes along to expose yet more potential failure mechanisms.
Does your product operate in the flat part of the curve? If so, how do you know? Is it assumed or do you have data and knowledge to support that claim?
Leave a Reply