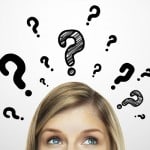
FMEA Q and A
In this Q and A article, a reader asks an interesting question about whether or not to update a System FMEA, when making subsequent changes to lower-level items. This is an excellent question, and shows the reader has good insight into the application of FMEA.
“Judge a man by his questions, not his answers.”
Voltaire
Reader’s Question
Can you please help me in understanding System FMEA with respect to the following questions?
I understand that for new product programs or new application of existing design, we perform System FMEA before the design gets frozen. However, this is not best followed for Continuous Improvement changes or small design changes. In those cases, sometimes Design FMEA gets addressed, but essentially may not address system issues. Here consideration is that, those changes may affect system functionality. Example is coolant composition change, flow pressure change for pump, filter element change, etc. Is there any objective evaluation criteria when to do System FMEA? How should this issue be addressed when evaluating small design changes, for System FMEA may require more resources and may not be feasible?
Consider the following hypothetical proposed changes:
1. Changing oil filter element material
2. Coolant composition change
3. Oil line O-ring groove depth dimension increase
4. Proprietary supplier of pump has changed some design parameters
5. Supplier suggested some changes in torque of seat mounting positions
Above scenarios are for making my query clear. Here my real concern is shall I perform System FMEA with all these changes proposed, as there may be some impact on other functional systems of vehicle? Or do you suggest some objective evaluation, so that it should give me some rating or decision on performing of System FMEA for each design change proposed. There should not be any confusion when to perform Design FMEA or System FMEA. What are your recommendations to handle these kinds of situations?
Answer to Reader’s Question
There are two ways that changes to product programs can be managed. Both will be explained below.
The first way to manage system changes is by updating the System FMEA and performing or updating any needed Design FMEAs. For new product programs, a System FMEA should be done as soon as system concept is determined, and completed (as you note) before system design freeze. The System FMEA can be subsequently updated when there are changes to the system configuration, as you describe in your question above. The System FMEA update should assess how changes to system configuration or components impact the system itself, as well as the interfaces between subsystems and/or components, and recommend actions to reduce risk due to the changes. The update to the System FMEA is not a new System FMEA, but merely a review of the current System FMEA to make needed adjustments. Your question on when to update a System FMEA can be answered as follows: when there are changes to the system configuration or componentry that impact the operation of the system itself, or impact the interfaces between subsystem and/or components within the system, it is a good idea to update the System FMEA. What sometimes seem to be minor changes to components or interfaces can cause significant system problems. In addition to the System FMEA update, individual Design FMEAs can be done (or updated) on the subsystems or components that have been changed. Not all changes justify a Design FMEA. Preliminary risk assessment can help identify which changes require Design FMEAs, and is fully covered in chapter 4 of my book.
The second way to manage system changes is through the use of Change Point Analysis and Design Review Based on Failure Mode (DRBFM). This presupposes that there is a properly done System FMEA to begin with. Here’s an excerpt from the book, which references an excellent presentation by Lisa Allen at the 2008 Applied Reliability Symposium.
A DRBFM project always builds from the success of a Good Design. Once the Good Design is established, the next step in a DRBFM project is called “Change Point Analysis.” It begins with the baseline design and focuses on the specific changes to the design. It is the initial step in Good Discussion. The main idea is to begin with a robust design and to fully understand and document all of the change points to the baseline design. Change points can include changes in design, manufacturing, supplier, supplier design or process, usage environment, interfaces, specifications, performance requirements, or any other changes.
Both Change Point Analysis and DRBFM are covered in chapter 13 of my book.
Next Article
Why do you think FMEA procedure requires effects to be taken to the system or end user? Why not describe the consequence only at the local level. If a bolt in a complex system fails, the parts that the bolt was clamping together may come apart. Isn’t that enough? The next article covers essential information about the effects of failure, along with examples and application tips.
Leave a Reply