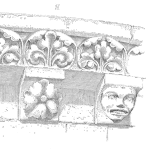
People build, transport, use, maintain and dispose of equipment or products.
Thus the creation of these items should include consideration of the humans involved. In order to fully benefit from the functional capability of an item or system, we, as humans, have to interact with an item’s interface, displays, sounds, etc.
Whether a smartphone or bottling machine, the ability to provide commands or direction, the ability to recognize and understand responses, and the ability to correctly identify faults or outputs all combine to permit humans to place calls or fill juice bottles.
It is in the design stage that the elements of a piece of equipment (hardware or software) thwart or enable efficient human interaction.
According to the FAA (Human Factors Design Standard: For Acquisition of Commercial Off-The-Shelf Subsystems, non-developmental Items, and Developmental Systems, by Vicki Ahlstrom, and Kelly Longo, DOT/FAA/CT-03/05 HF-STD-001, May 2003, Chapter 2) the following principles apply for the design or selection of systems or equipment:
Basic Design Elements
Make the System Durable — the equipment has to operate and be maintained within the expected set of conditions (environmental and use conditions)
Allocate Functions Appropriately — consider the differences between what the human or the equipment may accomplish given the performance requirements for sensitivity, precision, time, and safety. Consider factors of cost and skill level for both maintenance and operation.
Test with users — actual users in a realistic environment
Make the system reliable — the item should function over time in a specified environment with a specific probability of success in order to maximize availability.
Design for Simplicity — the design and interface should be as simple as possible while consistent with human-machine system interaction.
Minimize training — operation and maintenance activities should require only minimal familiarization and training to operate or maintain properly.
Make Functions Obvious — the equipment should not present puzzles or hidden controls for fundamental functionality.
Consistency
Make the Design consistent —this includes the appearance, behavior, and response through the system
Be Consistent with User mental Model — key to minimize training, employ an analogy with real life objects, employ conventions from similar systems, and follow patterns from previous operational experiences.
Minimize Inconsistency — on occasion it may be necessary to break consistency to support a specific task or function. Avoid using novel or unique approaches or mental models.
Standardization
Standardize hardware and software — specifically for the use of common user interfaces across buttons, dials, displays, colors, and related schemes.
Maintain Identical Interfaces for Identical Functions
Make Controls, Displays Marking, Coding, Labeling, and Arrangement Uniform
Make Appearance Distinctive — if the function is different that appearance should be different
Standardize Terminology, Look, and Feel
Make Functionally Similar Equipment Interchangeable
Make Functionally Different Equipment Non-Interchangeable
Safety
Incorporate Safety Factors — use an appropriate system and personal safety factors including those that minimize human error under normal, degraded, or emergency conditions and under adverse environments.
Provide a fail-safe design
Make Systems Error Resistant — as much as possible
Make Systems Error Tolerant — if it’s possible for a human to make an error, he will, thus the equipment should be detected, mitigated, or at least be resilient to possible human errors.
Warn of Potentially Unsafe Actions — before initiating a task that may have serious consequences
Identify Safe and Unsafe States and Actions — for example clearly identify danger posed by bypassing safeguards when troubleshooting or maintaining the system
Provide Emergency Procedures for Critical Systems — a clear step by step description of what to do in the event of a failure
Provide Redundancy — specifically for the access to the systems and equipment that provide a critical function
Design systems to be Modular — for ease of replacement and return to operation
Provide Warning Labels — increase awareness to avoid damage during equipment handling, installation, operation or maintenance.
Prevent Misalignment and Improper Mounting — include physical features that preclude improper mounting or alignment
User-Centered Perspective
This involves focusing on the needs and requirements of the end user throughout the design acquisition, or development process.
Provide Timely and Informative Feedback
Provide Predictable Results to User Actions
Use Familiar Terms and Images
Maximize Human Performance — foster effective procedures, work patterns, and personnel safety
Minimize Training Requirements
Design to Meet User Requirements
Minimize User Actions — specifically user hand and eye movements
Facilitate Transfer of Skills — this is from one experience to another based on consistency and standardization.
Design for 5th ago 95th percentile — of human physical characteristics, such as height, strength, perception, etc.
Accommodate Physical Diversity — this accounts for the myriad of human characteristics which do not imply a tall person will have a long reach, for example. While often not feasible to create a design that functions efficiently for everyone, it should at least accommodate for everyone to safely and efficiently perform their tasks.
Design to Accommodate People with Disabilities
Provide Enough Flexibility for different User Skill Levels
Maximize User Subjective Satisfaction
Support
Provide Help
Maintenance
Design for Common Tools
Make Systems Easy to Maintain
This is just a quick summary of the principles and supporting points. To learn more about these principles and more about human factor design guidelines, download the Ch2 General design requirements (PDF) or view the full document online.
Related:
Human Factor Considerations (article)
Comparing Human and Machine Capability (article)
Safety Factor (article)
Very nice write-up. My human factors reference has always been MIL-STD-1472. Steven.
Hi Steven, thanks and I wasn’t aware of the standard you mention. It is complete and detailed. It could easily be adapted for most any industry. Here’s a link to the download page. MIL-STD-1472