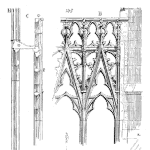
Written with assistance from Ben Karel of Fusion Engineering Plastics
Pty Ltd. Unit 1, 7 Dobra Rd, Yangebup WA ph (08) 9494 1004
Abstract
Welding can join thermoplastic parts together. It can be by melting the surfaces and pressing them together or by extrusion welding with a filler rod.
Several methods of welding are available. Proper manual techniques are critical to success as is the pressure testing of pressure parts.
Keywords: electro-fusion, butt welding, electro-socket welding, hot air gun, melt temperature.
Why Use Plastics?
Plastics have some wonderful engineering properties that can be used to great benefit.
- they handle a vast range of chemicals
- they don’t rust
- some of them are very slippery and little sticks to them
- they are extremely cheap compared to the exotic alloys
required to match some of the properties - they don’t transmit electricity or heat easily
- some are tough and will deform instead of breaking
under impact - they are so easy to fabricate that people can be trained in
a week to join plastics well
Their major drawbacks when compared to metals are:
- most soften at comparatively low temperatures
- they cannot take high tension continuously
- some can expand greatly when heated
- they break down in sunlight unless protected
The Two Families of Plastic
Plastics are broadly grouped into two distinct families – thermoset and thermoplastic.
Thermosets can only be molded once. After their first melt, they set permanently. A thermoplastic can be melted a number of times and the shape changed. Welded plastics are thermoplastics.
The difference between the two families of plastic results from how the macromolecules (See July 2000 article on Polyethylene) bond together at the atomic level. Thermoset molecules are triggered by heat to chemically react and join.
Thermoplastic molecules are attracted to each other but do not chemically bond. Figure 1 shows the difference in the type and numbers of bonds between thermoset and thermoplastic materials.
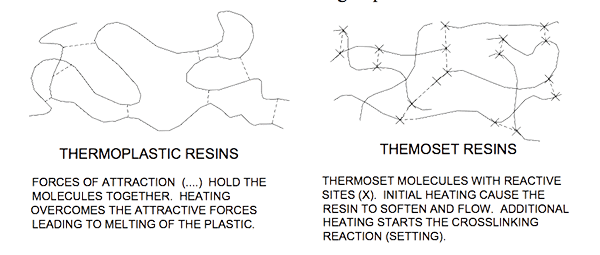
Heat Joined Plastics
The common plastics, which are joined together using heat, are PE (polyethylene), PP (polypropylene) and PVC (Polyvinylchloride).
At the exotic end, PVDF (polyvinylidene fluoride) and PTFE (polytetrafluoroethylene) can also be welded.
Joining Plastic Together
Heating the contact surfaces above their melting point and then pushing them together firmly till they set joins thermoplastics. When the molten faces come together the macromolecules intertwine and bond together on cooling.
The three critical factors for a good join are – achieving the right melt temperature; sufficient pressure when pushing the faces together; the length of time the join is allowed to cool before releasing the pressure.
Methods to Join Plastics Using Heat
Several methods are available to heat join plastics.
Butt-welding is used to join pipes. The pipe ends are held in a special clamping rig, then cut and faced square with a cutting tool. A hot plate set to the melt temperature is inserted between the two ends and the pipes pushed onto the hot plate.
Once enough time has passed to melt the pipe ends the hot plate is removed and the ends pushed together under pressure. After a time ranging from a few seconds to a few minutes, depending on the thickness of the pipe, the pressure is released.
The pipe is then left to cool down. This may take a few minutes for small-bore pipe and up to an hour and a half for large pipes with 50mm wall thickness.
Socket welding is done by using heated tools to melt the outside of the first few centimeters of a pipe end and the first few centimeters on the inside of the socket fitting. The pipe is pushed inside the socket and held in place till it cools.
Electro-socket welding is the same as socket welding except an electrical wire is installed in the fitting when it is made. The pipe is pushed into the socket and the wire connected to a power source. The wire heats up and melts the plastic surfaces. When the power is removed the plastic cools down.
Beware that the metal heating wire can come into contact with the process chemical in the pipe. If the chemical is incompatible with the metal it will corrode the filament and leak out along the wire track.
Extrusion welding is used to weld plastic sheets together. Plastic wire from 2mm to 6mm in diameter, depending on the size of the extruder, is fed through a heated barrel where it melts.
The tip of the extruder heats the plastic sheet and melts the surface. The molten wire in the extruder is forced onto the melted surfaces and joins the edges of the sheets together. The extruder is gradually fed along the joint melting the surfaces and laying the filler material as it goes.
Extrusion welded joints are de-rated to 80% of the parent material’s strength.
Hot air gun welding is used for light duty fabrication and tacking large fabricated items together before finally extrusion welding them. With this method, a hand-held plastic wire is pushed into the joint made by the corner edges of the two parts. The hot air gun is used to melt the corner edges of the plastic and the hand-held plastic wire.
The operator watches for the melt to develop and forces the wire into the weld. The hot air gun is kept ahead of the moving belt and the plastic wire continuously rolled forward into the puddle.
Cooling is rapid and by the time the operator’s hand passes a point the plastic has joined together.
Good Plastic Welding Practice
The secret to a high quality plastic weld is cleanliness.
Contamination must be avoided. For example, water will cause voids and bubbles in a weld. The contacting faces or edges must be clean. Before heating a butt or socket weld acetone is used to wipe the end of the pipe clean.
Recognised procedures need to be properly followed and operators trained and tested to the procedures. Most plastic welding procedures are based on German standards.
The quality of butt welds can be checked by tensile tests. A sample of a butt-welded pipe is held at each end in a machine and stretched. The force is measured and the weld must stay together up to the required load.
A spark test can be used to check extrusion welds. A voltage created by an electrically charged plate on one side of the sheet and an oppositely charged handheld wire brush on the other side will cause a spark to jump if a hole is present.
Good practice is to always test welds with water under full operating pressure. In the case of piping this will confirm its integrity and with tanks, it will locate leaks.
Mike Sondalini – Maintenance Engineer
We (Accendo Reliability) published this article with the kind permission of Feed Forward Publishing, a subsidiary of BIN95.com
Web: trade-school.education
E-mail: info@trade-school.education
Interesting, this can be a new solution for the welding industry.
I never knew that a certain change in macromolecules determines different thermosets. I also never knew that you can only set the thermoset once. I can see why you would need to be very precise in the welding.