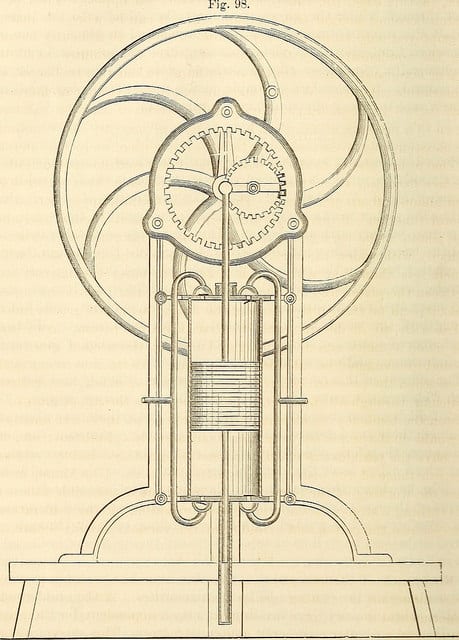
How to Translate Customer Expectations About Reliability
As a customer when I purchase a new car, a toaster, or a pump for my production line, I expect it to work. To Just Work. As a reliability professional, I also have the language to specify what I mean by, ‘just work’.
Customers that are not reliability engineers do not accurately specify what they mean by ‘it should just work’. So, we have to do a little extra to help translate that they want into specifications that we (manufacturer of the item) can create and deliver.
How Customers Ask for a Reliable Product
Customers typically do not specifically ask for reliability performance specifications. In some markets it is common though the request may be unclear. In either case, we should ask, “What reliability performance do you want?”
The quick and obvious customer response is they do not want any product failures. The product they purchase should function flawlessly for as long as they want to use the product. This is a difficult product to create.
Another common response is they want the product to just work. They have a time period in mind and be able to say, “the pump should operate for at least 5 years.” Or, the customer may indicate a desired MTBF or failure rate or quality level.
Customers may indicate the function and environment, yet it is rare they include all four elements of a complete reliability goal. Customers have a desired reliability performance, and generally do not provide sufficient information to specify what the actually want concerning product reliability.
Common Measures We Use to Specify Reliability
MTBF and similar metrics are common (not useful, as you know). I generally recommend avoiding the use of MTBF and similar measures.
Reliability is a measure. It has four elements (function, environment, probability and duration) and here let’s focus on the probability and duration elements. If we’re talking about a cell phone, we may specify reliability as 98% of units operate successfully (i.e. do not fail) for at least 2 years.
Another measure that customer may desire is uptime or availability. Reliability is a part of this measure and we require the same four elements within a fully stated reliability statement, plus information about repair times.
How to Translate What Customers Say to a Meaningful Specification
Let’s say a customer approaches you and wants to buy your product. They furthermore request that the product should just work. They actually say, “It should just work.” Then what do you do?
I recommend that you ask for clarification. Use the four elements of a reliability statement to understand the function(s), environment, probability and duration elements that the customer has in mind when they say “it should just work.”
Over what duration should the product work? If it’s a cell phone, they may say for a year, or two years, or they may expect it to work for 5 years. Ask them to be specific.
The probability is harder to ask for information directly. This generally has to be framed as the cost of the product to achieve a specific reliability or as a cost to the customer of a failure consequence, or both. If the request is for very high reliability, say 99.999% chance of successful operation over two years, the cost to create such a product may be orders of magnitude then one that has a 98% chance over the same period.
Would the chance of failure be acceptable given the difference in cost?
Likewise, would the chance of failure be acceptable given the cost of failure consequence. A product used in a safety or emergency situation most likely will have less tolerance for failures, while a less critical application may be fine with a less reliable product.
The discussion may include the underlying technology and details about the customer’s application. The intent is to define the probability of successful operation that is acceptable given the constraints. This in part will reflect the customers acceptance of the risk of failure.
One simple example has a customer specifying the desired reliability as 50,000 hour MTBF. So, we ask over what duration they expect to use the product. They respond with 5 years…. a quick calculation reveals that if the product as designed actually meets the exponential distribution assumptions and achieves 50k MTBF, they will expect approximately only a 1 in 3 chance that the product will survive the 5 years.
Is that what the want?
Maybe they do and they really understand the meaning of the MTBF specification as applied over the 5 year duration. Or, they may not. When rephrased in terms of probability of success as a percentage surviving, the request may not make sense.
So, ask, how many units should last 5 years, or what probability of survival for the product do they want (or can accept?). Well, they may want most or the vast majority to survive 5 years. Maybe they are using your product in a system that has a warranty provision. They can calculate an acceptable failure rate that permits achieving their business goals and still meeting their warranty budget.
Ask a few questions and use the duration and probability elements to help you customer articulate what they really want and accept concerning reliability.
How do you work with your suppliers or customers to understand the expected reliability performance? Leave a comment and share you best practices or frustrations.
Leave a Reply