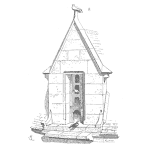
Read about the Requirements for the Content of the ISO 9001 Quality Manual Lead Document from which the rest of an ISO 9001 Quality System Cascades
An ISO 9001 Quality Management System requires a ISO 9001 Quality Manual that contains all the details of how your business is run to produce your products or services to a quality standard.
The ISO 9001 quality system standard does not require inclusion of other business processes not impacting quality, such as accounting, safety management, stationery, vehicle fleet management, etc, (unless your business is to provide accounting, safety, stationery or fleet management, etc—then you will definitely need to include them).
Best practice is to include every part of your business and every document into your quality management system (QMS). That way you are obliged to manage your business as the system of interacting processes that it really is. This is one of the secrets for real ISO 9001 business quality system success.
If you put some of your business into a ISO 9001 management system and leave out all the other parts of your business, you will treat your business as a disjointed entity. Your ISO9001 Quality System will be seen as a weight around your neck because you must ‘follow the rules’ imposed by ISO9001 accreditation, which you do not have to do with the other parts of the business not in the quality system. If you really want to make the ISO 9001 quality system standard to work for you then only have one way to run all of your business—using standardised and systematised processes.
To make the quality manual manageable, and in large organisations to make its sections small enough to pick-up and carry, the manual is divided by convention into a lead document from which all other documents stem, such as your procedures, work instructions, forms, spreadsheets, etc.
This lead document is commonly called the Quality Manual, and from it you can trace every other quality system document. There are particular contents of the lead Quality Manual to include when you develop it.
The lead Quality Manual is an introduction to your business quality management system and the processes, practices and documentation supporting the delivery of a quality product or service to customers. It is meant to give customers confidence in the products and in the business that makes them. It is also a marketing document that you will hand out to your customers, prospects, employees, suppliers and other interested parties as evidence of your company’s commitment to its customers’ satisfaction and to its business growth and lasting success.
In light of its function the lead Quality Manual needs to address and inform about the following:
- Communicate the vision, mission, policies and objectives of the organisation
- Explain the scope of the QMS, what parts of the business it covers and the value the QMS adds to the business
- Present a brief marketing portrayal about the benefits of the business and the advantages the products brings to Customers
- Include information on associated businesses, how they fit in the corporate structure, their locations, any outstanding features and benefits to the business, customers, QMS, etc
- Describe the range of applications that the products are meant to be used for
- Overview how the business makes its products and the processes used to make them
- Explain the management and organisational structure used to operate the business
- Introduce the system performance indicators used to measure the QMS efficacy and results
- Outline the business’ interested parties such as owners, employees, regulators, suppliers, etc
- Explain the linkages and interactions of the processes used to run the business
- Explain the linkages and interactions of the processes used to make the products and services
- Explain how the products and services are delivered to Customers
- Summarise any special machines, tools and devices and why they are used and the advantages they give Customers
- Advise where the products are geographically made
- Describe the competencies and any special skills and knowledge used to make the products
- Overview the Customer related processes used to ensure Clients are satisfied
- Introduce the product and/or service non-conformance and improvement process
- Describe how the business researches and innovates to better satisfy customers and attract new customers
- Outline how the business plans to remain in business to grow and satisfy its markets, and its past and future customers
- Explain the business risk assessment and risk management process
- Overview the document and records management and control process
- Summarise how human resources management apply to the business and brings benefits to its future wellbeing
- Summarise the physical infrastructure used to make products and run the business
- Provide the documentation framework for the rest of the QMS documents
- List the deployment matrices of the documents used in the QMS
- Advise what other management systems are used in the business e.g. safety, environmental, food health, etc
The lead ISO 9001 Quality Manual ranges in size from 30 to 80 pages depending on the extent of the business, the range of products and services provided and the complexity of the processes used for making products and ensuring their quality management within the business. Keep the lead quality manual easy to handle and pass about. Put all the details in other documents that you can send to people on request.
My best regards to you,
Mike Sondalini
Managing Director
Lifetime Reliability Solutions
Leave a Reply