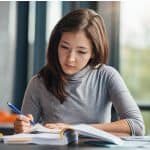
– a Key Step in FMEA Preparation
“. . . not everything that can be counted counts” Albert Einstein
A key, but often missed, step in FMEA preparation is to identify and prioritize the functions that relate to the item being analyzed. These become candidate functions to be brought into the FMEA.
Recall in an FMEA, “Item” is the focus of the analysis, and “Function” is the what the item is intended to do (including associated requirement(s).
If you haven’t read the Inside FMEA article on Functions, now is a good time.
Understanding FMEA Functions: the Essence of the Item
System and Design FMEAs must consider basic and interface functions, when preparing for the FMEA. Process FMEAs must consider the functions that relate to the process steps.
Basic functions are what the item is intended to do (including associated requirement). Interface functions are what the identified interface is intended to do (including associated requirement).
The challenge comes when there are many potential functions. Complex systems can have dozens of functions, and sub-assemblies and components can have many functions.
Do all functions need to be analyzed using FMEA procedure?
The short answer is “no.” It is up to the FMEA team (considering company policy and customer requirements) whether to bring in all functions to the FMEA or to prioritize the functions and bring in the higher priority functions. FMEA procedure does not require that every possible function be analyzed in the FMEA.
For example, a pencil manufacturer may choose to bring in the basic functions(s) of the pencil in the Design FMEA; but may choose to omit a function relating to providing a “No. 2” inscription on the side of the pencil. This is up to the pencil manufacturer and the FMEA team.
Why prioritize functions?
FMEAs can anticipate and prevent problems and help companies achieve high reliability in products and processes. However, they cost money, and every effort should be made to minimize the amount of time spent in FMEA meetings, while ensuring risk is identified and reduced to an acceptable level. It goes without saying that the integrity of the FMEA should never be compromised. However, there is no reason to consume time on low-priority issues.
Consider a sub-assembly where there are a total of 10 functions (basic and interface). Let’s say 3 of them are high priority, 4 of them are medium priority, and 3 of them are low priority. The FMEA team can choose to begin with the 3 highest priority functions, and, time permitting, continue with the 4 medium priority functions, while omitting the 3 lowest priority functions. Alternatively, the FMEA team can perform the FMEA on all 10 functions. However, in many companies, there is not sufficient time to include every possible function in each FMEA.
When companies broaden the scope of FMEA too far, the danger is FMEA not getting done properly, and becoming a “check box” exercise. Better to do an excellent job on the highest priority areas than do a mediocre job on everything.
Bicycle Hand Brake Design FMEA example
A project team is preparing to perform an FMEA on the next generation bicycle. They have scoped the project and one of the FMEAs that will be done is on the hand brake subsystem.
The FMEA Block Diagram looks like this.
FMEABlockDiagramExample-HandBrakeSubsystem
The team decides to modify the FMEA Block Diagram to visually show which of the blocks and interfaces are most important. Specifically, they color-coded blocks or interfaces with either significant field issues, new technology, or other risk criteria.
FMEABlockDiagramExample-HandBrakeSubsystemcolorcoded
The next step in the Hand Brake FMEA preparation is to create a list of possible basic and interface functions. Here is a fictional list, not meant to be complete.
Basic Functions:
Provides the correct level of friction between brake pad assembly and wheel rim to safely stop bicycle in the required distance.
Easy to pull brake level, with maximum pull force of X pounds.
Lack of noisy brakes, with maximum noise level less than Y decibels.
Interface Functions:
Brake lever to handle bar: provide sufficient clamping force to ensure no movement or change in orientation.
Brake pad to brake caliper: no movement between brake pad and caliper so that pad maintains correct orientation throughout all braking maneuvers.
The project team then prioritizes the basic and interface functions, considering criteria such as: past field problems, changes to the design, and new technology, along with the color coded FMEA Block Diagram.
In this fictional example, the FMEA team assesses the following priorities:
- Provides the correct level of friction between brake pad assembly and wheel rim to safely stop bicycle in the required distance. (High)
- Easy to pull brake level, with maximum pull force of X pounds. (Med)
- Lack of noisy brakes, with maximum noise level less than Y decibels. (Med)
- Interface: brake lever to handle bar – provides sufficient clamping force to ensure no movement or change in orientation. (Med)
- Interface: brake pad to brake caliper – ensures no movement between brake pad and caliper so that pad maintains correct orientation throughout all braking maneuvers. (High)
Next Article
The next article in the Inside FMEA series will be on the subject of pre-population of selected portions of FMEAs, including prioritized functions. By pre-populating the highest priority functions, along with other selected information, the FMEA team can focus their efforts on the most important functions, and minimize in-meeting time.
Application Tip
Always review the prioritized list of functions with the full FMEA team before commencing the FMEA. Ensure the full FMEA team agrees with the prioritization, and make any needed adjustments.
Reader Question
“In my company, we do FMEA (product and process) for all products. Is this a mistake? Should we focus FMEA’s only on products with novel content?”
My reply:
If your company has the resources to perform high-quality FMEAs on every product and process, that certainly can be done. In many companies, they do not have the resources to do high-quality FMEAs on every product and process. And if they try, FMEA ends up being a check-box, with less than high-quality results. In those cases, I recommend prioritizing FMEAs using preliminary risk assessment.
Here is an excerpt from chapter 4 of my book, Effective FMEAs.
FMEAs take time and cost money. They should be done when a certain level of risk can be effectively addressed by the FMEA procedure.
Some of the criteria to consider in determining whether to perform an FMEA include:
- Risk identified by System FMEA
- Potential for safety issues
- New technology
- New applications of existing technology
- History of significant field problems
- Potential for important regulation issues
- Supplier capability
Preliminary risk assessment provides a way to prioritize candidate FMEA projects. If your company has the resources to do FMEAs on all products, that is certainly possible. If not, the most important FMEA projects can be prioritized.
Leave a Reply