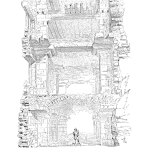
There are two instances when you should implement preventative action. First, once a failure occurs and you would like to avoid similar future failures. Second, before a failure occurs, yet an undesired failure mechanism is likely to occur.
Like corrective action there is a wide range of possible preventative actions. The selection of the right actions requires considering customer expectations, business and legal factors, along with the technical and economic feasibility.
Types of Preventative Action
Preventative actions by their definition are done on equipment that has not yet failed. The system may be actively operating, temporarily taken off line, or in a quiescent period.
There are many types of actions including:
- Testing
- Measurements
- Adjustments
- Parts replacement
- Cleaning
- Alignment
These actions may be scheduled or done with each use. Scheduling may be by calendar time, or by operation milestones (hours of operation for example)
Customer Expectations Concerning Preventative Action
The level of understanding concerning maintenance for a product varies both by customer and by type of product and system. Most buyers of a passenger vehicle realize the car requires regular addition of fuel (or electricity), yet may not fully understand the need for lubrication, alignment, or tire rotation.
Some customers fully understand and expect to conduct preventative maintenance, while others do not. The design of a system has to incorporate the common approach to preventative maintenance while safeguarding the product from those that ignore such action.
Asking customers to check tire pressure or oil level with each fill up of fuel while still in many car owner’s manuals is rarely done. Modern vehicles include both an engine oil level warning light, plus a set of tire pressure indicators. These dashboard sensor readings are measurements that provide information that may initiate preventative maintenance as needed.
Business and Legal Considerations
Businesses tend to desire the creation of profit. The ability support a system in the hands of customers may require staffing a call center, stocking spare parts, or providing preventative maintenance services directly. The management team must consider the ongoing costs to support the preventative maintenance as part of the initial business case for the new product offering.
Legal obligations differ by region, country, and industry. The ability to avoid failures with preventative maintenance is not often regulated, yet having the ability to properly, and safely, maintain equipment may fall under one or more jurisdiction.
Technical and Economic Considerations
In some cases it is possible to select materials or design that eliminate the need for preventative maintenance. Sealed bearings, for example, preclude the need for routine servicing. Some applications permit such solutions, while others do not given other design constraints.
The ability to balance the ongoing costs of inspections and servicing with the costs of robust designs the reduce the need for maintenance is done with tradeoff analysis to meet business objectives and customer expectations.
The understanding the failure mechanisms permits the exploration of the appropriate preventive actions. If an item slowly wears, a periodic inspection and measurement may provide a means to accurately predict the time for replacement. In other cases the ability to test using highly specialized equipment may be the only option. In each situation the expected failure mechanisms dictate the range of preventative actions available.
Another factor is who pays for the maintenance costs. What is customary or factored into the purchase price? What is the industry expectations for a specific type of equipment? In some cases, shifting the cost one way to the other may provide a market advantage.
Selecting the Appropriate Preventative Action
From testing, alignment, to replacement, the appropriate preventative action depends on many factors. Innovation continues to provide additional options. The integration of sensors provides an great way to employ prognostic health management tools.
Which ever set of actions are available select the one or more action that provide an economical and safe solution for your system. In critical areas, use a set of actions that provide a overlapping set of tools to permit the safe continued operation of the system.
How have you seen preventative maintenance change over the past 10 years or so? Are you now using techniques previously not expected nor economical?
Leave a Reply