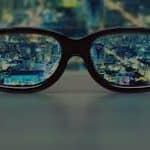
The importance of reliability education in a product development program cannot be understated. A design initiative with mechanical content can be created solely by the mechanical team, same for electrical, and software. These other disciplines will create a better product if they collaborate from the start, but this is not necessary. A successful product can still be created if they intersect later. Reliability doesn’t have this flexibility. Reliability tools don’t have a deliverable like a function or a feature. They are an assist for the function or feature during the process of creation. As an assist discipline, it only works if implemented while the other processes are in motion. Attempting to add it after the design has been completed requires a deconstruction of the previous work if improvements are needed.
Take for example the design of a mechanical system like an automotive transmission. A mechanical engineer will create gear, casing, and bearing designs to ensure the product has the correct functions. In the design process factors like force, torque, and temperature were fundamental considerations. Let’s assume the design is complete and now reliability performance is considered. What can be done? We will start with reliability tests that measure the performance of margins, manufacturing, use-case, and environment variabilities. We find that the case has fracture points with even minor manufacturing or use variability. This will likely result in a percentage of population failure when in widespread use. To correct the issue the case will have to be modified. These strengthening modifications may change the ability for heat dissipation to be sufficient. To accommodate the needed heat dissipation either the power transfer requirement or spacing for gears will have to be changed.
This is a great deal of adjustment and accommodation for improvement of only one robustness against variability. If the case’s sensitivity to the primary use and manufacturing stress had been identified in the early design phase through risk analysis and test tools, a fundamentally different case would have been created. The mechanical design process that included design for reliability (DfR) would have had features that improved heat dissipation throughout the entire part and provided strength only where it is most needed to handle variation. The gear, bearing, shaft designs would have been created based on the optimal case design, and not victims of a shifting landscape.
For this inclusion of reliability analysis in the design process all disciplines must have knowledge of how reliability test and analysis tools can be applied. It is not reasonable to expect diligent designers to know how to incorporate these tools if they are unaware of how they work or how they can affect design. The investment in reliability education for the team in advance of a program yields an ongoing increase in design process efficiency that can’t be understated.
-Adam
Join the Apex Ridge Mailing list.
Visit www.Apex Ridge.com to learn more about our services.
or send me a message to say Hi! at abahret@apexridge.com
Leave a Reply