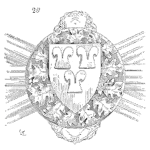
Derating is the selection of components and materials according to a set of standardized safety-margin definitions.
It is used by design engineers to ensure the selected elements of the design do not experience performance problems due to overstress conditions.
Derating, like stress-strength analysis, assists the designer when selecting elements for the product or system.
The outcome is a robust design able to withstand the expected, and some of the unexpected, stress applied.
The derating process
Start with a derating guideline.
Note: derating guidelines are typically listed with information for electronic components, yet the concept applies to a mechanical element as well. For mechanical systems, we generally use safety factor or margin guidelines, not derating guidelines.
There are a number of derating guidelines publicly available.
Your organization may revise an existing guideline or craft one for use in your applications.
A comprehensive guideline is SD-18 compiled by the Navel Sea Systems Command, NSWC Crane Division.
MIT published a guideline for EE-INST-002 in 2005.
Component vendors typically provide derating guidelines for their products.
For example, Kement provides voltage and temperature derating guidelines for their line of capacitors. Voltage and temperature derating guidelines – Kemet
There are derating guidelines from standards bodies, from space agencies and military organizations.
In a study we did at HP when updating our internal derating guidelines, we found the various guidelines generally agreed with each other.
The key for the derating process is to have a documented set of guidelines and to enforce the routine use of the guidelines.
A typical derating guideline and how to use it
From the NavSea set of guidelines, the derating guideline states:
Maximum Allowable Rating:
Current/Voltage — 80%
Power — 50% (See Notes 1 and 4 below)
1. For repetitive pulse applications, the average power is determined by dividing pulse duration by duty cycle, and multiplying the result by the peak power.
4. Derating values for thick film resistors is taken from IPC-MC-790, “Guidelines for Multichip Module Technology Utilization”; August 1992.
To use this information consider the situation where you wish to use a thick film capacitor on a circuit with a nominal 5 volts applied across the capacitor.
You may be able to find a capacitor rated by the vendor for 5 volts.
This is the vendor’s rated voltage. Thus in an application using 5 volts, it would experience the voltage stress that is 100% of the rated value.
This is above the derating guideline and to be avoided.
Instead, let’s do a little math.
We need to find a capacitor with a rated voltage that is high enough that the applied 5 volts are at 80% or less the rated value.
If we divide 5 volts by 0.8 (the guideline 80%) we find 6.25 volts.
Our capacitor vendor may not provide a solution rated at exactly 6.25 volts, which is fine. This is our minimum rated value to meet the guideline.
So, if we find a capacitor rated at 10 volts, that should work for our situation. The application voltage of 5 volts divided by the rated value of 10 volts shows we are at a 50% derated condition.
This is below the maximum allowable and fine.
The same process applies for current and power.
Each component may have one or more parameters to consider for derating. The selected component should satisfy each piece of the guideline.
The best approach to apply the guidelines is during component selection.
For items that may violate the guideline or are simply close the maximum recommendations, that is a prompt to understand the risks involved.
The derating and reliability discussion
The guideline is, well, a guideline.
There will be times you need to select a part which violates the guideline.
The guideline should prompt discussion and understanding of the risks involved when selecting a component which doesn’t meet the guidelines. Even those which are close, yet strictly do meet the guidelines, should prompt further consideration.
The elements at or above the derating guidelines have little to no margin.
They may work and may work well for your specific application.
It’s just the recommended margin is less, thus that part will not be capable of withstanding the variations in:
- Applied stress
- Manufacturing
- Transportation and storage
- Installation
- Power line
- Environment
- Use
Every component in your product will experience a broad range of stress variation.
Having ample margin helps your system operate with fewer failures.
Summary
As your organization employs a derating guideline, your product will become more robust, and reliable.
The higher rated parts may cost a bit more, yet the savings through fewer failures and happier customers is ample return on the investment.
It does take some discipline to adhere to a set of derating guidelines. With a bit of training and practice, it really doesn’t take too much effort to make it happen.
The added benefit of identifying potential weaker elements of your product may assist you and your team better characterize the reliability risks within the design.
Do you and your team use a derating guideline? How well is it working? What are some of the difficulties you’ve seen?
Leave a comment, join the conversation.
Leave a Reply