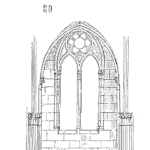
Environmental testing is the evaluation of a product or system in one or more stress conditions. Environmental as in that which surrounds and affects a product. Consider temperature. Is the product going to experience outdoor temperatures as found in Fargo, North Dakota or Belmopan, Belize?
The weather is one way to describe external stresses, yet it is so much more. Environmental testing may include fungus, insect, and animal exposure. The document MIL-STD-810G lists and describes testing methods for a wide range of environmental conditions.
In addition to weather during operation be sure to consider how the product is stored, transported, and installed. Also, consider the effects of different phases of use. For example, an aircraft has ground operations, take-off and landing sets of stresses, plus level flight. Each is quite different.
Why do environmental testing?
A great way to test a product in its operating environment is to conduct beta testing. Essentially place the product in normal use and ask for feedback or monitor performance. In the hands of those expected to use the product in ‘the wild’, we can learn how the design responds to the many known and unknown environmental conditions.
In practice, beta testing is expensive and time-consuming. So, many conducting testing in the lab with one or more stresses applied to a product. Again this can be a costly and time-consuming practice.
Environmental testing has a number of functions:
- Reduce uncertainty concerning the designs ability to function in the expected environment.
- Detect environmental stress induced weaknesses to allow design improvements
- Determine robustness beyond the expected environmental conditions.
Basically, we conduct environmental testing to determine if the product will function as expected when exposed to a range of conditions.
Environmental testing and reliability
Reliability is the ability of a product to function as expected within an environment with a probability of success over a duration. Very similar to environmental testing with respect to will it operate in an environment.
The primary difference is the lack of evaluating the product over the expected duration. Most environmental testing is fairly quick – I.e. Will the product operate when exposed to 40°C for 1 hour? Not will it work for 20 years when expected to experience 40°C on occasion each year.
They are related though. Defects or weaknesses found during environmental testing may lead to reliability improvements. In general, a robust product tends to be more reliable. The environmental conditions may represent the stresses that may be useful for life or reliability testing. Environmental testing findings may lead to the understanding of failure mechanisms that are essential to design an accelerated life test.
Recommendations
Conduct environmental testing to reduce uncertainty and to quantify margins.
Be prepared to learn how to improve the design.
Do not directly conclude that a design that passes a suite of environmental testing is also reliable.
Leverage environmental testing methods to design accelerated life testing when suitable for specific failure mechanisms.
It’s interesting that you talked about how you can see if a design will be affected by the environment it is in. I have been planning a project, and I was wondering if I should get an environmental test first. I can see how it would be smart to have done, so you can become aware of any potential problems with your design.
Hi Scott, before planning for the testing consider gathering information about the use environment and use conditions. This information along with a risk analysis may help guide the design process…. for areas that have high risk or unknowns, focus the environmental testing not those areas to get the most value from your prototypes. cheers, Fred