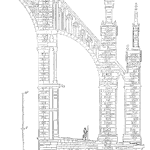
It is rare that a third party generated FMEA/FMECA has any value. The development or manufacturing teams and supporting staff should comprise the bulk of the study’s team. Team size for a specific study would include 4 to 10 individuals.
The FMEA/FMECA should provide clear action items that may include:
Conduct research or experiments to understand and quantify uncertainty. This may include exploring how an item responds to specific stress, errors or inputs. Or include experiments to estimate the occurrence rating for a specific potential cause of a failure mode.
Explore alternative solutions that would thwart potential failure causes, mitigate or avoid consequences of a failure, or improve the ability to detect and avert potential failures.
The FMEA/FMECA study should include clear boundaries, focus on preventing initiating cause or avoiding resulting consequences. Inspections, testing, and other detection techniques should be a last resort option.
Studies that start with an item’s bill of materials with the exhaustive study of each item’s potential impact on system performance should be avoided. These studies are tedious and rarely provide any meaningful insights for the development team. Instead, conduct multiple studies with appropriate team members for specific scopes and aims.
For example, as functional requirements become available, study the impact of potential failure modes at the functional level using the plan of record technology. As detailed designs become available, conduct focused studies on subsystems or major components, especially those related to previously identify high-risk areas.
Each team may adjust their scoring to meet the needs of the specific study. Keeping notes on scoring scales permits other teams to later modify the study using a similar scoring system.
The intent is to prioritize actions not to adhere to a fixed scoring approach. An FMEA/FMECA with little no separation of RPNs does not provide guidance for improvements.
Summary
While not an exhaustive set of performance criteria – hopefully, you can use the ideas here to plan and conduct valuable studies.
Leave a Reply