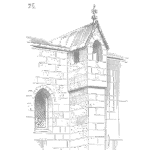
See www.jsaprograms.com for innovation in hazard control.
Doing a job safely is no accident! Like all good outcomes safety is a result of good planning. As the Chinese philosopher Confucius said, “In all things success depends on previous preparation and without such preparation there is sure to be failure.” If you want safe work it needs to be planned as part of the job.
The other important fact about safety is that it is a personal responsibility. It is up to you to do the job safely. There is not a manager or supervisor in the world that wants to go to prison or be fined for a death or maiming because of his negligence. That means people in-charge want jobs done safely too. All they ask is that the safety procedures and practices used on the job be the least that are adequate while still meeting all the safety issues.
So what are the least suitable and adequate safety procedures and practices to use on a job? You won’t like the answer because it is not always clear. The answer is ‘It depends on the job.’ This means each job has to be assessed for the safety risks in contains and suitable and adequate practices and procedures put into place to control each risk
For the majority of jobs the normal two or three person minimum communication and confirmation practices of tagging-out and signing onto permits (such as permits-to-work, hot work permits, excavation permits, confined space entry permits, working at height permits and their like) will cover a large portion of job safety concerns. However they may also not be sufficient and adequate for a particular job. It is necessary that the additional requirements for safe work be recognised before the job starts.
To help recognise safety issues before they arise on a job a Job Safety Analysis (JSA) may need to be performed. A JSA is a documented step-by-step safety action plan that lists the individual job tasks, the risks in each task, the consequences of the risk and how each risk will be managed to insure the safety of personnel. Creating a JSA involves a meeting between the people who know the plant and its processes with those who will be doing the work.
It is possible to identify the hazards before a job starts and put actions into place that improve job safety. By getting together the people who have knowledge of the plant with the people who will do the work many risks can be immediately eliminated.
The output from a JSA is a document that tells people how the work will be done safely. Once the safety plan is ready it must be told to all people involved with the job so they can work together to insure a safe result.
Mike Sondalini – Maintenance Engineer
We (Accendo Reliability) published this article with the kind permission of Feed Forward Publishing, a subsidiary of BIN95.com
Web: trade-school.education
E-mail: info@trade-school.education
If you found this interesting you may like the ebook Bulk Materials Handling Introduction.
Leave a Reply