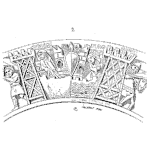
A gearbox is used to control the operating speed of industrial equipment.
It converts a high input speed to a lower output speed and so permits one driver element, such as an electric motor, to do numerous duties.
Failure of the gearbox causes the equipment and associated plant to stop.
Proper selection, care, and maintenance of gearboxes is critical to your company’s continued profitability.
Gearbox selection
A gearbox is selected for the duty it must perform.
Each selection must take consideration of the following points.
Load type |
|
Environment |
|
Forces |
|
Robustness |
|
Drive |
|
Gear type |
|
Maintenance |
|
Operations |
|
For example, in the selection of a gearbox to be directly coupled to an agitator for a stirred tank, consideration must be given to the distance the output shaft bearings are apart.
Bearings positioned further apart cope better with the bending forces generated by the paddles located at the end of the agitator shaft.
The load type will affect the selection of the gear type.
Steady, continuous loads can be accommodated by spur gears but impact loads can break spur gear teeth.
A more robust gear to use in impact load situations would be a helical gear.
This gear shape offers more tooth cross- sectional area and because of the helix dissipates impact forces axially and tangentially.
Another style of gearing often seen on slow moving, high load applications are the worm and worm wheel.
Planetary gearboxes are available where space is limited for standard design gearboxes.
Gearbox care
A well-selected gearbox will have a long service life.
Long-term maintenance will involve checking oil levels and for critical or expensive gearboxes checking oil quality.
Oil quality ought to be tested at least every two years for stationary plant and every year for a mobile plant. More often if the loading or service duty is arduous.
A simple site test for gearbox oil is to take a sample and look at the color, note the smell, look and feel for the presence of grit and feel the slipperiness compared to fresh oil.
If you are concerned then send a sample to a lubrication test lab.
Choice of lubricant is critical
The oil must retain its properties at the operating temperature.
The gearbox manufacturer is best able to advise the oil to use. Where the manufacturer cannot be contacted, one of the major oil companies can offer practical suggestions on the oil to use.
Mixing of different oils in the same gearbox is poor practice.
Unless you can tell the oil supplier with certainty what oil is already in the gearbox so a match can be specified, do not cross mix oils. Mineral and synthetic oils are not compatible.
It is better to drain the old oil out, flush the gearbox through with the new oil, put in the new oil to the required level and run the gearbox for two to three hours and finally dump, flush and refill the gearbox again.
Breathers
Breathers are fitted to prevent shaft seals blowing out as the internal pressure rises when the gearbox is warming up to operating temperature.
A breather allows moisture in the air and dirt from the surroundings to enter the gearbox.
Locate and protect the breather to reduce the risk of contamination.
Check with the gearbox manufacturer to see if a breather is needed and if not then do without it.
Overload conditions
Unexpected high working loads can occur that will destroy gearboxes.
For overload conditions shear pins can be installed in the drive train or motor overload protection can be fitted to the power supply.
For those services where impact loading is normal such protection is mandatory.
Orientation
A belt or chain drive gearbox should be oriented so the forces in the drive pull the gearbox down onto its feet.
Where the orientation of the gearbox causes the gearbox to be pulled off its feet there is a risk the feet will break from fatigue caused by fluctuating loads.
In this case, additional clamping of the body may be necessary.
Gearbox maintenance
When a gearbox is open cleanliness is critical.
Dirt and dust entering bearings and gear teeth spaces will cause wear and rapid failure.
If gears with chipped teeth are reused, chamfer the chipped edges to remove loose metal.
Gearbox bearings may require pre-loading to a minimum bearing load to prevent excessive noise and wear.
Pre- loading bearings ensure the rolling elements are properly bedded onto the races and prevent the rolling elements skipping and sliding around the tracks.
Mike Sondalini – Maintenance Engineer
We (Accendo Reliability) published this article with the kind permission of Feed Forward Publishing, a subsidiary of BIN95.com
Web: trade-school.education
E-mail: info@trade-school.education
If you found this interesting you may like the ebook Process Control Essentials.
Leave a Reply