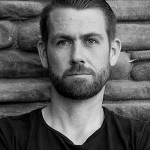
First Steps with Data
Abstract
Chris and Fred discuss what is the first thing with you do when someone gives you lots of information. What do you do?
ᐅ Play Episode
Your Reliability Engineering Professional Development Site
by Christopher Jackson Leave a Comment
Chris and Fred discuss what is the first thing with you do when someone gives you lots of information. What do you do?
ᐅ Play Episode
by Christopher Jackson Leave a Comment
Chris and Fred discuss how reliability data analysis really doesn’t mean a lot … unless you pair it with a failure mechanism. Why is this? What does that mean?
ᐅ Play Episode
by Christopher Jackson Leave a Comment
Chris and Fred discuss what it means to have incomplete data. Isn’t data just data?
ᐅ Play Episode
by James Kovacevic Leave a Comment
It’s my pleasure to welcome back Peter Horsburgh. He is the author of the ‘Five Habits of Extraordinary Reliability Engineers.’ He has a long history within reliability engineering. He essentially started in manufacturing, then moved to mining, then to power generation, and to aluminum smelting.
In this episode we covered:
by Adam Bahret Leave a Comment
Adam discusses how data can be used from existing databases and specially designed tests to characterise products reliability performance.
ᐅ Play Episode
by James Kovacevic Leave a Comment
With the advent of Industry 4.0, data and connectivity have enabled equipment to become continuous factories of data. Whether process data, master data or realtime data, it has never been a more challenging time to adjust and harness the power of seemingly huge piles of potential information. Traditional maintenance and reliability are undergoing a tremendous shift as organizations become more data-driven. Sean Rosier and Nathanael Ince of PinnacleART are on the show to help us put in context, the relevance of data in reliability.
ᐅ Play Episode
by James Kovacevic Leave a Comment
Failure data is very important for leaders to make effective and efficient decisions. That’s why they are always looking for industry best practices and new implementation techniques to understand failure codes and failure modes in a better way. The organizations always focus on understanding failure codes so that they can design their CMMS. They always configure their CMMS to better analyze the failure data. They have a process in place that allows them to run failure data against different fields based on the failure codes. Failure data must be synchronized to hold RCM analysis results. CMMS can be built in way that it perfectly serves the purpose.
In this episode, we covered:
by Adam Bahret Leave a Comment
Adam and Fred discussing how data influences design and program decisions.
ᐅ Play Episode
by Adam Bahret Leave a Comment
Adam and Fred discussing the challenges of acquiring reliability data and it’s value to a program
ᐅ Play Episode
by Tim Rodgers Leave a Comment
Tim and Fred discuss the feedback loop that connects field performance to the production processes at the supplier, and how advanced sensing technology provides more data to all parties, but doesn’t necessarily lead to greater knowledge or improved reliability.
ᐅ Play Episode
by Adam Bahret Leave a Comment
Adam and Fred discussing the dilemma of too much data in an organization and not enough for reliability work.
ᐅ Play Episode
by Adam Bahret Leave a Comment
Adam and Fred discussing the often interesting, challenging and sometimes frustrating tasks before actually analyzing the data.
ᐅ Play Episode
by James Kovacevic Leave a Comment
In today’s episode, the guest Fred Schenkelberg explains the Monte Carlo simulation in a fair amount of detail. Before you get in the depth of how the tool works, you need to understand what basically this method is. The Monte Carlo simulation has been around since World War 2 and it is a mathematical technique that works based on probability functions, random variables, and the distribution of statistical data. The main concept of it to give the decision maker the most obvious choices while facing any risks to get the best out of every possible outcome. The tool serves the purpose for getting a better insight of the consequences relative to each choice the person making decisions has to make. When you’re looking for the reliability of your assets and checking the integrity of your different maintenance programs, it is a really powerful tool.
ᐅ Play Episode
Kirk and Fred discussing the difficulty of getting the failed products, especially low cost systems, back from the field to do failure analysis on.
ᐅ Play Episode
In today’s episode, the guest is John Reeve and the agenda of discussion is failure data and CMMS. As everyone knows that to maintain and solve issues with the equipment you need to get all the basic data or information available. Computerized maintenance management system helps greatly in this task but first of all, you have to know exactly what kind of data are you looking for and what it means. Now failure data can be anything related to your asset that is the foundation data or then transactional data comes which includes the processing data related to the asset such as the actual cost. Now, next thing to understand is the failure mode which consists of the failed component, component problem and cause code. Once you have this failure data, it becomes very easy to run the basic failure analysis which is necessary at certain levels.
ᐅ Play Episode