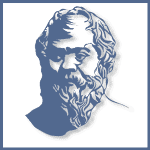
Bob Latino Author
Tim interviews Bob about EasyRCA, Reliability and Safety.
Your Reliability Engineering Professional Development Site
by Tim Rodgers Leave a Comment
by James Kovacevic Leave a Comment
by James Kovacevic Leave a Comment
RCA is one of the most basic yet most important of the processes in a reliability program. RCA isn’t just about solving a problem or fixing an error in your system. It is more than just finding a single root causes. When a problem occurs, there can be more than one reasons why that occurred in the first place. RCA helps us reduce the risk of that problem to a level that is acceptable to the organization. It is always a systemic and latent approach that takes time and should be done more often rather than just doing it when a problem has already occurred.
In this episode, we covered:
RCA is a process where you get to the root cause of the problem and then solve it by using a systemic approach. To get started with RCA, you need to gather your data first. Once you set your data points to gather meaningful and useful data, then, you can perform RCA to prevent a failure or find a solution to fix it. There are four basic steps for a good RCA. In the first step, you should be able to gather fresh data the minute a failure occurs. In the second step, you have to determine the impact of that incident. You should know what you are looking for?
In this episode, we covered:
The organizations often tend to ignore some simple things when they are mitigating a machinery failure. Some of the important things being; why did the failure occur? Who should be asked about it? What kind of measures can be taken so that it doesn’t occur again? Most of the time, it is just changing parts without doing the proper analysis or troubleshooting for that matter. What you should be doing as a professional organization is, train your technicians about step by step problem solving by giving them test examples. The technicians should be able to contribute to the solutions and they should be encouraged to do so.
In this episode, we covered:
by James Kovacevic Leave a Comment
When you deal with machines on daily basis, machine failures are bound to happen. But what if these failures keep occurring? Wouldn’t you get tired and want a solution for these problems? This is why root cause analysis is so important in an organization. The basic idea of RCA is to know the reason behind the occurrence of a failure and then finding a solution to reduce a risk—certain or uncertain—in a cost-effective manner. You can’t just rely on a single approach all the time because it might not be applicable to your problem.
ᐅ Play Episode
by Fred Schenkelberg 2 Comments
The ability to determine a root cause of a failure is a skill. It requires agility, leadership, inquisitiveness, diligence, and technical skill. Successful RCA taps into your creativity and technical prowess. Using a structured approach helps.
[Read more…]
by James Kovacevic Leave a Comment
It happens all the time that when certain companies can’t solve a problem, they just move on and overlook it. Sometimes, they successfully solve the problem but it keeps reappearing because they don’t have a proper process for solving that problem. That causes a lot of downtime and costs a lot in the long run. They spare all these resources for solving the problem quickly without even looking for the origin of the problem—the root cause—that they don’t even write the solutions applied in an understandable and applicable way for the next time, the same problem occurs.
ᐅ Play Episode
by James Kovacevic Leave a Comment
This episode of the rooted in reliability podcast covers the Root Cause Analysis in the light of a book written by Susan Lubell – the guest herself—and the book is part of the made simple series. In this book, Susan has covered a number of matrices that need to be answered very specifically and clearly based on the methodologies adopted by different organizations. This book doesn’t just focus on the terminologies and specific techniques that are used by the experts. It actually covers the very baselines of the RCA methods such as how to get started with the analysis and what to look for in order to successfully implement it. This book is more of a guide for those who want to start their journey in the field and can use a bunch of best practices that are used by the top-notch organizations in the industry. It’s not about the fault tree analysis or other techniques that are used to determine the root cause. It’s more about the people managing side of the Root Cause Analysis like why do you need to perform an RCA and what are the factors that drive it.
ᐅ Play Episode
by Carl S. Carlson Leave a Comment
Carl and Fred discussing the reliability tool called “Root Cause Analysis,” and how RCA can be used in reliability programs.
ᐅ Play Episode
by James Kovacevic Leave a Comment
In today’s episode, the topic of the discussion is 8D problem solving. When it comes to problem-solving, there are a lot of procedures and techniques out there but what most of the engineers and reliability professional use is the Eight Disciplines problem solving. It is step by step approach to finding the root cause of the problem and then resolve it effectively and systemically. To perform this method, you need to have a team of different experts in place as it is not the job of a single person. Then, you can start solving issues in the following steps.
by James Kovacevic Leave a Comment
This episode is based on the discussion on Root Cause Analysis also known as RCA. It is a technique which is used to solve complex problems when finding the origin of any failure gets difficult. RCA includes a series of steps that lead right to the place from where the problem originated.
ᐅ Play Episode