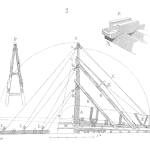
SOR 523 Getting the Best from Your Root Cause Analysis
Abstract
James discusses the story of the one machine that was causing a lot of grief.
ᐅ Play Episode
Your Reliability Engineering Professional Development Site
by James Kovacevic Leave a Comment
James discusses the story of the one machine that was causing a lot of grief.
ᐅ Play Episode
Reliability Centered Maintenance or RCM is a philosophy that is rooted in the fundamentals of the reliability and maintenance. There are seven steps or principles of RCM that can really help you do RCM correctly. The first four steps of RCM make up FMEA and when you combine the next two with these, it gives you a FMECA baseline. With these seven steps, you can do all the wonderful things that make up a successful reliability program. In RCM, functions are where you start your journey. A function can be defined as what you need from a piece of equipment.
In this episode, we covered:
RCM principles have been around for nearly 50 years now, and its process for nearly 40 years. Surprisingly, there is still a wide misconception and most people still don’t understand the term that is RCM. So, what is RCM or Reliability-Centered Maintenance? RCM is one of the most efficient and effective proactive maintenance processes that is considered one of the most powerful asset management tools. One of the great things about RCM is that you can apply it to any industry or your daily life. It has one of the most diverse applications in the world.
ᐅ Play Episode
by James Kovacevic Leave a Comment
Ever wonder why your assets aren’t producing the value they are supposed to even if you have trained staff and big budgets? Are you a fan of Predictive maintenance improvement of your organizational processes? Then, condition monitoring is where you should start. The meaning of this word is as simple as the word itself. You just need to check the state of your asset on a regular basis and as the state of your asset change, you would know what possible failures that change can lead to and then you can try predictive maintenance strategies to stop that failure from occurring in the first place.
ᐅ Play Episode
by James Kovacevic Leave a Comment
In this episode, the guests, James Reyes-Picknell and Jesus Sifonte talk about the RCM Reengineered that they have also explained in their book—to be launched on 20th April— with a lot of practical approaches as well. The RCM Reengineered is based on the original RCM technique to avoid and manage failures occurring during the asset management process, but it optimizes a lot of factors with a broad range of criticality measures and problems that come along with it. The RCM has been around for a long time and was developed to handle the safety issues in flights but RCM Reengineered focuses on the failures that are science-based and then it provides you with the exact solutions that must be implemented to achieve long-term and sustainable reliability operation depending upon the type of the industry.
ᐅ Play Episode
by Fred Schenkelberg Leave a Comment
by James Kovacevic Leave a Comment
This episode of the weekly podcast covers the 4 Pitfalls of OEM Recommendations.
The original equipment manufacturers provide a manual in which all the general instructions are provided in the form of an operating manual.
These can be helpful when someone is using the equipment for the first time but when the same apparatus has to be used in reputed organizations with a set-up of their own, this manual is not enough.
It is developed keeping in mind the general behavior of instruments and common environmental condition of workshops and laboratories.
Most of the times, manufacturers put together these recommendations considering the worst that can go wrong to cover their warranty policies.
That is why the organizations cannot rely only on this operating manual.
ᐅ Play Episode
Review RCM is a streamlined approach to improving plant performance.
It allows organizations to quickly address ineffective PM programs. How does it achieve this?
By using the operating environment, failure patterns, and P-F interval, we can answer three basic questions:
These three elements will help us to determine the type of PM strategy that is value-added.
ᐅ Play Episode
by James Kovacevic Leave a Comment
Does the age of equipment increase the probability of failure?
That was the conventional wisdom until Nowlan & Heap discovered that components have six different types of failure patterns:
This means only 11% of failures are age related… 89% are not age related – so why do PM Programs still rely on time-based maintenance (Replacements, Overhauls) they only address 11% of failures.
ᐅ Play Episode