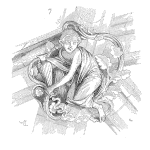
Suppliers often include reliability information along with performance specifications.
We look for reliability statements as one part of the selection process to ascertain if the component is likely to have sufficient reliability.
When the vendor’s data is clearly stated and meaningful, that information saves us from potentially having to conduct our own reliability evaluations.
Let’s say we are exploring purchasing sealed bearing for a front tire of a new model of bicycle.
We expect the bearings reliability should be at least 98% reliable over 1 years with regular exposure to 40°C ambient temperatures.
We find a couple of options online and examine the data sheets.
Bearing Vendor A
The data sheet only provides the following statement concerning reliability.
MTTF 75,000 hours
Nothing else.
Is this good enough for our application? Let’s find out.
With no other information than MTTF we should use the exponential distribution to estimate the bearing reliability at one years.
$$ \large\displaystyle \begin{array}{*{35}{l}}
R\left( t \right)={{e}^{-\frac{t}{\theta }}} \\
R\left( 8,760 \right)={{e}^{-\frac{8,760}{75,000}}}=0.8897 \\
\end{array}$$
Where t is time in hours and a year has 8,760 hours.
And, $-\theta-$ is the MTTF value given by the vendor.
The result is disappointing. According to this information and the assumption of an exponential distribution, we would expect about 11% of the units to fail over the year.
Bearing Vendor B
The data sheet references a life document on the vendor’s website which contains the following reliability information.
The bearings primarily fail due to the breakdown of the bearing grease.
The grease breakdown (the document includes a definition of failure, which references in increase in start to movement resistance) follows a Weibull distribution time to failure distribution at 25°C ambient.
The Weibull parameters are $-\beta-$ = 2 and $-\eta-$ = 75,000 hours
We can use the reliability function for the Weibull distribution to estimate the probability of successfully operating over a year as follows
$$\large\displaystyle \begin{array}{*{35}{l}}
R\left( t \right)={{e}^{-{{\left( \frac{t}{\eta } \right)}^{\beta }}}} \\
R\left( 8,760 \right)={{e}^{-{{\left( \frac{8,760}{75,000} \right)}^{2}}}}=0.9865 \\
\end{array}$$
This is better, yet notice the parameters apply with a 25°C ambient temperature.
We expect the bearing will see a sustained temperature of 40°C. So, reading further in the vendor supplied life document we find a formula to translate the characteristic life, $-\eta-$ for different temperatures.
Without going into the details of the math associated with the provided formula we determine the $-\eta-$ value is reduced by 0.95, thus becomes 71,250 hours.
Recalculating the reliability at one year, we find at 40°C it is 98.5% reliable.
Vendor Selection
With just the information from the data sheets, supporting documents, and a little math the selection of the bearing based on expected reliability performance is clear.
The direct calculations show that one vendor will not meet the target reliability using the given information.
It is likely that Vendor A knows about bearing grease wear out and the relationship between temperature and characteristic life, yet choose to list the often requested and simple MTTF value.
Unfortunately, that leaves the reader to either make a few assumptions or spend time investigating if there is additional reliability information available.
The Vendor B data provided a clear means to calculate reliability for our conditions.
Even if the results didn’t meet our requirements, working with Vendor B would be my choice.
They seem to understand what is expected to fail, have done the characterization work, and freely share the reliability information.
They may have an alternative solution that would meet our needs (if needed).
The idea here is to use the vendor provided reliability data to estimate the reliability performance under your expected conditions.
Then compare to your reliability apportioned goals.
Related:
The Next Step in Your Data Analysis (article)
Confidence Interval Interpretations & Misunderstandings (article)
Basic Approaches to Life Testing (article)
Leave a Reply