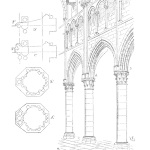
Most senior managements don’t know that Reliability can get them high profits very quickly. And therefore high return on investment. Hyundai’s Ten Year Warranty. Their market share was going downhill for over ten years, suddenly it started to go upwards instead. All because of high reliability!
The impact of reliability extends far beyond reliability itself. It establishes the cost of warrants, repair, maintenance, logistics and the indirect costs of unavailability, downtime, and the COST OF SAFETY RECALLS which runs to hundreds of million dollars., and throughout the life of the product. This paper presents an outside-the-box view of how to get the best results by aiming at twice the life in the product specification and by preventing the high-risk failure modes resulting in an extraordinary return on investment, as much as 10,000%.
Right Way to Reliability
As we are all aware, some companies, besides Hyundai, have built up a long reputation for reliability such as Toyota, Microsoft, Airbus, Harley-Davidson, and several aerospace companies. Most often, companies do not use consciously reliability as a competitive advantage as a marketing tool. Someone offering a ten-year warranty or promising high availability could easily grab considerable market share, by applying the right effort at the right time. Unfortunately, most of them go through too many failures and dissatisfied customers before they achieve high reliability. The most horrible mistakes they make is to start out with a terrible specification of writing poor performance specifications where about 60% requirements are missing! It is hard enough to do the right things, but it is even harder to know what the right things are!
The Right Things to Do
Reliability is a process. If the right process is not followed, results cannot be right. The companies will be under the impression that they are following a process and doing the right things. However, the results could be far from what they imagine
Based on my experience of 30 years in reliability engineering, the following are some of the right things:
- Mission failure is not an option — component failure is.
- Aim at twice the life — because it is cheaper.
- Aim at for times the life for safety critical components
- Reliability must be in the product definition.
- Reliability definition must include “shall not”.
- Watch out for sneak failures.
- Reliability must be in the manufacturing process definition to prevent early failures.
- Reliability must result in cheaper, faster, and better products.
- Traditional budgets are illusions — use intuition.
Brief Description of the Right Things to Do
Mission failure is not an option
When I say no failures, I am talking about no mission failures. The mission for a driver is to complete the trip safely without noticeable downtime. A component can fail without causing the mission to fail. That is one reason why redundancy is built into critical functions, in hardware as well as in software.
Aim at twice the life — because it is cheaper
I always talk about “Twice the Life — No Failures — 500% ROI.” The simple answer is that it is cheaper because there will be practically zero warranty costs. Those who understand this paradox and take advantage of it are the real masters of reliability. I helped a company in Milwaukee that was going out of business because they lost over 50% customers. The customers expected 10- year life. We designed for 20 years because Engineering 101 recommends 100% design margin. We got all the customers back in two weeks by giving them a 15-year warranty!
Aim at for times the life for safety critical components
Customers often use products such as automobiles, airplanes, microwave ovens, and refrigerators beyond their expected life. If products are used as much as the second life, safety-related components must work much beyond that. The law requires that manufacturers are responsible for safety no matter how long a customer uses the product. Navy has a standard policy of four times the life for safety-critical components.
Reliability must be in the product definition
The product functions are often vaguely defined. There is often nothing in the specification about modularity, high reliability, safety, serviceability, logistics, human factors, diagnostics capability, or prevention of warranty failures. Very few specifications address even obvious requirements, such as internal interface, external interface, user-hardware interface, user-software interface, and how the product should behave if and when a sneak failure occurs. Those who are trying to build reliability around a faulty specification should only expect faulty reliability.
Reliability definition must include “shall not”
The specification must be clear on what the product should never do, however stupid it may sound. For example the SUV shall not roll over in case of a component failure or low tire pressure” or “There shall be no sudden acceleration in the moving vehicle.”
Watch out for sneak failures
This analysis is often ignored. It aims at failures that are difficult to predict. The sudden acceleration experienced by Audi 5000 when put in reverse gear is a typical example (took place years back). This analysis is informally called “Unknown Unknowns Analysis”. It should be performed before approving the preliminary design.One tool for this kind of analysis is called “Sneak Circuit Analysis”. This is used for discovering hidden problems, which usually turn up in rare events, such as the deployment of airbags, or when there is a major accident in which a fireman may come in contact with high voltage battery terminals.
Reliability must be in the manufacturing process definition to prevent early failures
The failures that occur within a few days of use are super early failures. Products that are dead on arrival (DOA) are good examples. These are sure to upset customers. More than 95% of the time, they are due to lack of manufacturing control, such as assembling a wrong part, loose connections, improper torque, and improperly aligned assemblies. Then there are failures in the first 2-3 years. They are called early failures. The cause is again in manufacturing. Design engineers must perform Manufacturing Failure Mode and Effects Analysis before releasing the specifications that prevent manufacturing related failures.
Reliability must result in cheaper, faster, and better products
Companies erroneously believe that making products with higher reliability costs more money. Actually, the opposite is true, if you really understand the art and science of reliability. The computer industry has demonstrated the truth of this. Computers have become steadily more reliable while also becoming less expensive. The cycle time is months instead of years. It does take more up-front effort but it drastically reduces the time it takes to put out fires.
Traditional budgets are illusions — use intuition
If you are going to make 700 changes in the specification, as in the case of the 1995 Lincoln Continental, then the initial budget is obsolete. We need the power of intuition to foresee unknown unknown problems. With so many changes the scope of the project has changed; you require a new budget, a new schedule, and a new contingency budget. Most companies, since they write poor specifications, do not see this problem. They keep adding one requirement, one at a time and fail to adjust the budget. Then they have to take short cuts to save money and time.
Conclusion
There are three kinds of organizations. Those that make things happen, those that watch things happen, and those that wonder what happened. If we write holistic specifications and perform a thorough analysis, then we don’t have to wonder what happened. We make things happen our way.
References
Raheja, Dev, Assurance Technologies: Principles and Practices, McGraw-Hill, New York,1991.
Raheja, Dev, There is Lot More to Reliability Than Reliability,” SAE paper , 2004, https://saemobilus.sae.org/content/2004-01-1286/
Leave a Reply