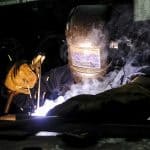
Maintenance Provides the Key Function of Preserving
With the design FMEA complete, the equipment should have high inherent reliability. The equipment can then be installed in the plant, and provide a high level of performance to the business, at least initially. This is where Maintenance comes in. Maintenance can enable a low Life Cycle Cost, by preserving the reliability of the equipment.
Definition of Maintenance
According to the Professional’s Guide to Maintenance & Reliability terminology, maintenance is “all actions necessary for retaining an item in, or restoring it to, a specified condition”. In other words, maintenance is the process of keeping the equipment in condition that is as good as new.
Why is this important? It identifies one important thing, Maintenance cannot improve reliability, as it is designed into the equipment. Often time’s maintenance is tasked with improving reliability, and there is little they can do to do so. But maintenance is critical to supporting the inherent reliability of the equipment.
How Maintenance Supports Reliability
Maintenance supports reliability by ensuring the equipment is maintained to as good as new condition. To do so, maintenance should follow a few best practices;
- Effective Maintenance Strategy – the strategy should be based on the consequence of the failure, not the failure itself. RCM2 and other techniques are great in identify the right strategy.
- Procedure Based Maintenance – is used to minimize variation in the activities, ensuring a consistent and reliable way of performing each task. This reduces errors in the task and enables greater availability.
- Make Reliability Part of the Culture – Maintenance alone cannot ensure the equipment will always be in as good as new condition. It requires a partnership with operations. Operations has to own the equipment as well.
When these practices are put into place, the equipment is maintained in as good as new condition, enabling a high level of availability.
How Can You Improve Reliability
If you are struggling with the reliability of the equipment, how do you go about improving it? There are a few different options to do so, which may involve maintenance. But maintenance is not solely responsible for;
- Redesign – do not try to PM out repetitive failures. Identify the root cause and end them once and for all.
- Procedures – ensure procedures existing for maintenance activities, and operator activities such as start-up, shutdown, and routine operation.
- Training – building the capability of your people is critical to the long term sustainability of the operation. Ensure operators know how to run the equipment, and ensure maintenance has the right technical skills to do so.
- Strategy – revise the plant strategy and involve operators in maintenance, define Root Cause Analysis triggers and act on them.
All these add up to reducing the total life cycle costs, which is the next topic in this series by Fred Schenkelberg.
Do you expect maintenance to improve the reliability of the equipment? Certainly they can improve the availability of it and reduce the consequences of the failure, but maintenance can’t improve the reliability of it.
Remember, to find success, you must first solve the problem, then achieve the implementation of the solution, and finally sustain winning results.
I’m James Kovacevic
Eruditio, LLC
Where Education Meets Application
—
The other articles in the series include:
Post 1 – Incorporating Reliability into Your Future
Post 2 – Using a Design FMEA
Post 3 – Where Does Maintenance Fit Into Reliability?
Post 4 – Life Cycle Costs
Post 5 – Close with Q&A
—
References:
RCM2 by John Moubray
Professional’s Guide to Maintenance & Reliability terminology
Root Cause Analysis Made Simple
The Basics of FMEA by Robin E. McDermott
Image Credit:
U.S. Naval Forces Central Command, “USS NIMITZ (CVN 68)_130923-N-AZ866-282”
Leave a Reply