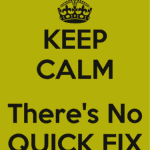
There are no quick fixes
Today’s world contains a myriad of choices for instant gratification.
Regardless of our age, we have grown used to getting what we want, when we want it, and how we want it limited only by our ability and willingness to pay for it.
Middle age and younger generations have grown up in the digital age with internet, email, instant messaging, cell phones, smartphones, VOIP, electronic games, virtual reality… More-so than older generations, they expect things to happen quickly.
In our day-to-day life, we’ve got it pretty easy as well as quick.
That carries over into the work environment, for some of us, at work there is a crucial difference – at work is where we conceive, build, test, operate and maintain the infrastructure and systems that make that day-to-day life so easy and so instant.
Ideas can happen quickly but just about everything else takes time.
Consider that most industries involve some sort of operational activity delivering something of value to customers (good or services).
Behind the scenes that delivery infrastructure must be kept operating. Whether it is a wired or wireless network, a piping system, a factory full of robotic production stations, a mine with trucks and ore processing or… operations are not possible without some sort of equipment.
That equipment can and will break at some point. When that happens, operational personnel are under intense pressure to restore service or production – management expects it to come back almost instantly. Operators in most (if not all) industries have similar expectations of maintainers. Yet maintainers have a different view.
Maintenance managers have a different view
We maintainers know that once something is not working, it can take a long time to restore to service, depending on what is wrong.
There are many things that could be wrong too – so even identifying the problem can take time. Most failures occur randomly so we don’t always know what’s about to hit us. Once the fault has been identified it may require special skills, knowledge, parts, tools, support equipment, and so on, in order to be corrected.
We know that getting all of this in place at the right time and in the right quantities to do the job quickly takes preparation – and that takes time. We can take steps to speed that up (good planning done in advance, good forecasting of parts requirements, etc.) but in our world, very little is instant – it all takes time. We can put that time in ahead of the need (proactively forecasting what will be needed) or reactively after the need arises.
In the latter case, we often find ourselves rushed and under intense pressure from everyone else who expects instant results.
Engineers build redundancy into critical systems so that functionality, once lost, can be restored almost instantly so that the inevitable repair can be done without loss of delivery capability.
Planners can plan work that will happen in future so there is no wait for a plan. Spare parts inventories can be built up on the basis of forecast future demands.
There is much we can do to shorten response and resolution times, but that preparation work requires time too.
There are no quick fixes
We cannot get around it – we live and work in a field of endeavor that enjoys little in the way of instant gratification and we struggle to understand why others don’t “get it” when we say we need time.
There are no “quick fixes” that will last for any length of time in our world.
Just as there are no quick fixes to satisfy the immediate needs of operations, there are no quick fixes to our own delivery capability when it needs to be improved or corrected.
Maintenance management itself is not something we can “fix” quickly if it is broken or failing to perform.
A good measure of maintenance performance delivery capability is “schedule success” (or “schedule compliance” if you prefer). In order to accomplish what you want to get done to a schedule that forecasts when you will do it, you need to have a number of processes working well.
If you are not scoring well, then one or more of the following may be in need of attention:
- Scheduling of work
- Planning of the work
- Work execution effectiveness
- Availability of materials, parts, and consumables
- Communication between planning, scheduling and materials management
- Adherence to work priorities
- Work identification
- Follow-up learning and feedback from work that is completed
- Supervision of workforce
- Motivation of employees
- Proactive maintenance program effectiveness.
Any one of those can take a lot of effort to correct – training, understanding, process design, systems support and even motivation of those involved. Recognize too that all of these work together to deliver that “schedule success”.
If one or more are not working well, it will have an impact on the others – they’re inter-dependent.
None of this can be corrected in an instant
There are a variety of programs, systems, methods and tools you can choose to help in addressing failings in any and all of these areas.
Yet, even if weak in only one area, the inter-dependent nature of all of these will inevitably mean that a failing in one area has created weaknesses or workaround processes in other areas.
For example, weak planning will leave materials managers in the dark about what materials are needed to support coming work.
Parts availability will appear to be poorly managed. They will buy what is regularly demanded and stop buying what they see is not used. There is a degree of self-correction built into the interaction of processes, but maintainers will undermine it with the best of intentions. Because they can’t get what they want, when they want it from stores, they will buy it as a direct purchase.
They will also buy an extra one for the next time. They will build up their own unofficial stores of parts. This activity distorts the inventory control picture quite dramatically because the movement of materials is simply not tracked if it doesn’t go through the inventory. Usage rates are distorted, actual parts needed are not identified and the inventory gradually becomes less and less relevant to what is really happening in the operation.
Fixing all this requires more than just a fix to planning, even though that is where the problem began.
Likewise, ineffective proactive maintenance programs can suffer from poor work identification, no consideration of reliability in making decisions, poor scheduling and compliance, etc. You may even have problems with operators who are operating equipment outside of the envelope in which it is intended to operate, leading to premature failures.
There are many potential causes to be explored and possibly corrected.
Conclusion
Recognize that if you’ve got an uptime maintenance regime that is failing to deliver reliability, higher than desired maintenance costs per unit of output, poor compliance to its own schedules or a lack of schedules, then you’ve got more than quick fix on your hands.
There simply are no quick fixes and no one solution is likely to get you what you want. You will almost always need to look at an array of activities that must be executed together or in some sequence to get you there.
To learn more visit Conscious Asset where you will find training, workshops, books, and resources.
Related
Preventive Maintenance “PM” Programs – Part 1 – The Basics (article)
Rapid Proactive Maintenance Program – PM Program – Part 3 (article)
Leave a Reply