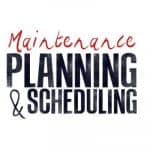
The relationship between maintenance planning and scheduling is similar to that of love and marriage, peanut butter and jelly, or bacon and eggs. It’s difficult to have one without the other. Each of these vital disciplines influences the other. But each is a distinct and separate process and, when performed properly, not really a feat of engineering but more an art form due to the vast number of activities required.
The disciplines for maintenance planning and scheduling are among the premises leading to the utilization of CMMS programs. It is helpful to have a solid, proven manual system in place for planning and scheduling before embarking upon utilization of a CMMS program for planning and scheduling. If a well-defined and functioning manual system exists, it makes the transition to the computerized system easier and more understandable.
Maintenance Planning
When planning, the basic questions the planner should ask are as follows.
- How would I do this job?
- What tools would I need?
- What assistance would I require?
- What equipment is needed to perform the work?
- How long will this job take?
- What supplies and or materials do I need?
- What safety precautions should I observe?
- Do I have detailed written documentation how this equipment is intended to operate and function?
- Is there a valid work order covering this required work?
- Can the equipment/asset be scheduled out of service long enough to accomplish the job requirements?
Maintenance Scheduling
The individual undertaking maintenance scheduling should be a good communicator, and have authority to discuss and authorize work with their counterparts in operations and production.
- Can the equipment be taken out of service on a specific date?
- Does the operations department have other activities that will have an impact on the planned work?
- Are adequate manpower and qualified personnel or contractor services available?
- Have I double-checked on the storeroom materials and ordered needed items?
- Are the other needed tools and special equipment, such as lifts and mobile cranes, available on those dates or are they assigned to another job or out for servicing?
Maintenance Planning and Scheduling Work Together
If the maintenance department currently does not plan or schedule work and is mostly a reactive work force, dependent upon the size of the organization, the addition of a qualified and talented planner/scheduler will improve the overall performance of the maintenance department by a factor of three (3). When performed correctly, the impact of the planner/scheduler function will be very noticeable for the maintenance department.
When undertaking the planning function, the planner should not attempt to plan sitting at a desk, but should view the equipment and surrounding area first-hand and talk with the operator or user. The scheduler must communicate well with others and gain agreement for items such as equipment outage and make all necessary arrangements for additional personnel and support equipment.
While these two disciplines are distinct, they can be combined with one person assuming both responsibilities. The risk for combining this function is that work may be properly planned but not scheduled, or scheduled but not properly planned. In either case, there will be adverse effects from the limited work effort such as:
- Job took too long because the workers did not know what portion of the total job they were responsible for performing.
- Necessary parts were not in stock or ordered.
- Operations did not know the work was scheduled and equipment was not released to maintenance.
- Not enough maintenance technicians were available due to many tasks during the same time period, vacations, etc.
- Necessary support equipment was not available, broken or failed to start.
The issues above are examples of items that should be addressed to ensure the desired work is performed correctly and in an expeditious manner. Planning and scheduling, whether via paper or CMMS software, are important to maximize the overall maintenance effort and improve the profitability of the company.
Keep in mind the following overall points:
- If you’re not properly planning, then don’t schedule.
- Don’t attempt to schedule work that you haven’t planned properly.
- If you are properly planning, then proceed to schedule. (Again, it’s difficult to have one without the other.)
DPSI specializes in maintenance management software solutions that help organizations manage, monitor and control maintenance. Our CMMS and EAM systems can streamline work order management and help organizations save time and money. Get started with a CMMS free trial today.
Leave a Reply