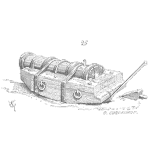
The very best asset managers have maintenance under control.
Their entire organization’s systems and methods are tuned to preventing unplanned stoppages. They only do that which has first been thought through and prepared for.
But most importantly they understand the key factor to excellent asset care and work toward it continuously and energetically.
Keywords: preventative maintenance, reliability-centered maintenance, RCM, total productive maintenance, TPM.
The “universal solution”
The universal solution to that poorly answered question of “What makes world class asset management?” was given serendipitously to me during a conversation about what makes a world class maintenance organization.
It’s a question that many have tried to address but have only resulted in baffling people with theory, science, and opinion and so totally missed the point.
The truth is clear and simple to understand.
It was so startlingly simple when it was said that I almost dismissed it, but was clearly obvious when thought about at greater depth.
It’s so straight forward in the concept that any and every company can start achieving world class performance in a very short time after they firmly grasp the revelation divulged that day.
It completely explains what world class asset management is all about and how the truly successful companies achieve their world class results.
With this revelation there is now a universal strategy to adopt that will work in every company and industry.
Plan preventative maintenance
It is simply that breakdowns overwhelm, but preventative maintenance can be planned. And planned work is the least expensive of maintenance strategies.
The world-class asset management organizations get their preventative maintenance up to more than 80% of their workload.
This then is the clear and straight path to world class asset management – strive to turn your maintenance around so that the vast majority of it is preventative.
Practice good asset management
Of course the best use good-practice asset management.
They have a corporate asset policy from which the production and maintenance objectives are generated and the performance measures derived.
All of which is followed up with an audit process to check the degree of success in achieving the objectives.
Document, document, document!
The best practice asset managers take a lifetime view of their business. They document why and how they will use their assets to achieve their business goals.
The documentation flows through the company to every level of the business defining, explaining and guiding people in their daily tasks and decision-making so that everyone’s actions are aligned to the lifetime business aims.
The people in those companies know what they have to do; why they are doing it and the benefits that come from their efforts.
There is plenty of documentation now readily available that gives clear guidance on what is required to achieve world- class asset management performance.
The most obvious and well-known one is the ISO9000 quality systems series. Others include the maintenance excellence award programs available from several organizations around the world.
By following the recommendations listed in those systems a company will go a long way toward achieving asset management excellence quickly.
Enhance reliability
The good practice asset managers select reliability enhancing tools such as Reliability Centered Maintenance, Weibull Analysis and the like, which they need to improve their position.
They use reliability enhancing systems and methods like Total Productive Maintenance, Kaizen continuous improvement, condition monitoring and their derivatives.
They proactively pursue low equipment failure strategies and practices.
Supply and procurement
The supply and procurement practices used in world class operations can be summed-up in a few simple words.
They work at buying the right materials at good prices, they have a high number of stock turnovers and they use supply contracts to their advantage to reduce business risk and develop proactive suppliers. They contract to the ‘best of breed’ suppliers and get the experts to look after specific types of equipment.
Examples are using Original Equipment Manufacturers to service the complicated equipment and going to specialist, quality contractors to supply and repair routable equipment such as valves.
They may even outsource their warehousing and stock control to key suppliers under clearly understood performance based contracts and pay the contractor only for the stocked equipment actually used plus an annual management fee.
The supplier manages and maintains a supply of critical spares on consignment at key locations in readiness for emergencies.
PLAN – long term
The world class players are great planners.
They have a minimum 5-year plan that is cascaded down to 1-year plans then to monthly plans of major events and finally daily plans. The planning is done in detail for all activities.
They check their own performance and review it weekly using Key Performance Indicators to learn what can be done better so that they continuously improve their results.
They plan widely and deeply to maximize the ‘wrench time’ of their tradespeople and get great workforce efficiencies.
When equipment failures occur they are analyzed to find the root cause and corrected so that they will not reoccur. They have a life plan for their assets – long-term plans and short- term plans.
They know how much money they should be making from each asset and can justify the expenditure to keep their assets up to a specified level of performance.
They use multi-skilled maintenance teams and develop the capabilities and abilities of each member in a supportive and encouraging environment.
Mike Sondalini – Equipment Longevity Engineer
We (Accendo Reliability) published this article with the kind permission of Feed Forward Publishing, a subsidiary of BIN95.com
Web: trade-school.education
E-mail: info@trade-school.education
If you found this interesting you may like the ebook Process Control Essentials.
Leave a Reply