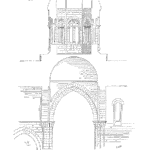
Welcome to part eight of my 10-part series of blogs called “Uptime Insights”, where we explore a journey of excellence in maintenance.
To stay on top, managers must implement strategies that keep operations performing at high levels. In these articles, I will show you how to achieve excellence in maintenance – a critical business process in any capital intensive industry.
Uptime Insights Part Eight:
Asset Reliability
Being proactive with your assets is all about managing failures before they occur.
You can reduce or eliminate the consequences of failure by forecasting what is likely to happen and deciding in advance about what to do about it. The advantage to doing this is that major business impact due to equipment breakdown can be avoided.
High performing companies manage proactively – they foresee and avoid problems.
It’s good for business!
Reliability Centered Maintenance
Reliability Centered Maintenance (RCM) is the most proven proactive approach for developing maintenance programs from scratch.
It is a logical process that can be used during the design stage of an asset’s life cycle or later after the asset has entered service. It uses the knowledge we have of how things fail as discussed in 4, to arrive at logical decisions for individual asset failure management policies.
The intent is to avoid or minimize the consequences of failures.
One of the great strengths of RCM is that it does not require failures to have occurred in order to generate data for analysis – it anticipates the most likely failure modes and deals with them and their consequences before the fact.
Programs developed using RCM provide for the safe minimum amount of appropriate proactive maintenance. These programs provide a balance of cost vs. reliability that is tailored specifically to your assets in your operating environment.
The tendency to over- or under-maintain, often a result of using other methods, is avoided.
RCM was developed and first proven in the aircraft industry where reliability really mattered and was quickly adopted for use in nuclear power generation. Today RCM is used in all capital intensive industries where reliability is important.
It is the cornerstone of any reliability improvement program.
How to be successful with RCM
The keys to success in RCM are the careful application of the process itself and follow-up by implementing the results in your maintenance program.
Many failures of well-run RCM programs occur because the outputs of the analysis are not put into practice in the operational environment. The follow up is critical.
Optimizing the maintenance program after it has been put into place is done on a continuous basis.
RCM isn’t perfect
If you want high reliability at optimum cost, RCM is the answer but even RCM is not perfect. Some unforeseen failures may still happen and you will want to avoid having them happen again.
Future equipment failures can also be eliminated through several reactive methods of asset reliability improvement. These methods are used after the failures have already occurred.
Post-mortem analysis can teach us a great deal. And, even if you have used RCM, there may be some failures you miss – in those cases, reactive methods are the answer.
Preventative Maintenance Optimization
Preventive Maintenance Optimization (PMO) is a method based on RCM logic that is applied to existing maintenance programs in an attempt to optimize them.
PMO arose out of the need to improve the performance of existing maintenance programs that were failing to meet desired performance expectations. RCM logic is used in analyzing the various maintenance activities of the existing program in order to eliminate or modify them.
It attempts to identify failure modes that may have been missed by the original maintenance program but its approach is not as thorough as RCM.
Nevertheless, it has achieved some very good results and it is worthy of consideration.
Root Cause Failure Analysis
Root Cause Failure Analysis (RCFA) is entirely reactive to failures that have already occurred.
RCFA is a method of performing a sort of “post mortem” to determine what caused any particular failure.
The intent is to eliminate the “root cause”, that being the identifiable cause that you can manage in some practical way.
Decision Optimization
Decision optimization techniques and tools help maintainers to make fact based decisions or to improve on decisions already made.
RCM can be used before the asset is put into service (as it is in the aircraft and nuclear industries) so the decisions made about task frequencies and failure modes were invariably made with some degree of uncertainty.
Once the program is put into place some failures will arise that were not anticipated or the frequencies of failures may be different than what was originally estimated. Optimization techniques are used to analyze the in-service data to validate or modify the original decisions.
It’s a form of second guessing, though much more precise, due to the failure data that has been accumulated in service and is now available for use.
These techniques can be very accurate provided the data is accurate and they are perhaps one of the best approaches for continuously improving on an existing maintenance program.
Summary
Reliability and simulation modeling are computer based techniques that allow us to mathematically model the behavior of our installed systems.
They can reveal where we have process bottlenecks and if we are working to improve on one bottleneck, where the next ones are likely to arise.
These models can also show us the effect of various reliability improvements at different points in the systems and help us focus our engineering efforts more effectively.
In our next blog, we’ll explore part nine of our 10 part series “Uptime Insights: Teamwork Produces Superior Results.”
Or you can download the entire series in our eBook “Uptime: A Journey Of Excellence.
How about predictive maintenance or Condition Based Maintenance (CBM)based on the POF predictions of the original design. Do you address these method in your next two blogs in this series?
Hi Tom,
From what I’ve seen of Jame’s series is he doesn’t get into the connection between PoF and predictive or CBM approaches. Maybe you could either add details in a comment or send me a guest post explaining the connection.
Cheers,
Fred