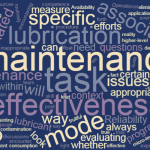
I am a firm believer in the notion of doing everything with the end-goal in mind. That is the only way we can gauge the effectiveness of our efforts. The same is true for all our efforts related to Maintenance & Reliability.
If & when you want to measure a certain maintenance task for its effectiveness (you should be doing it quite often); the best way is to identify whether the desired outcomes associated with that specific task are being realized or not.
Remaining within the context is always important when evaluating any business process. In case of the maintenance task(s); the context is provided by the specific failure mode(s) for which it has been adopted. The logical way to evaluate the effectiveness of a certain maintenance task(s) would be to look at the fact that whether the associated failure mode(s) have been eliminated or reduced.
For example, you can only evaluate the effectiveness of your lubrication task if you look at the specific failure mode(s) associated with lubrication only. If you are not encountering those failure mode(s); your lubrication task is effective.
You cannot evaluate this task for any failure mode(s) other than those associated with it. Let’s say you do encounter lubrication related failures then you will be required to do an analysis of your lubrication task. This may lead to several questions such as:
- Is the task carried out properly?
- Is the frequency of the task appropriate?
- Is there a need to review the procedure?
- Is there any contamination issues related to the lubricant? Storage & handling issues?
- Is the lubricant appropriate in terms of your application?
- What is the skill level of maintenance personnel performing the task?
- …. & so forth
Many times, we lose the sight of our actual objectives by painting a gloomy picture of our entire Maintenance program over a large canvas. When in reality the issues might be lying at a more micro-level.
Trying to evaluate the effectiveness of a maintenance task through higher-level KPIs & measures such as MTBF, Availability, MTTR, Spares consumption, Cost, Overall Safety or Operational Risks etc. will always be misleading. They are useful for an overall assessment of your Maintenance & Reliability program; but definitely inappropriate when evaluating specific maintenance task(s).
This also casts a light on the need to have technical & functional expertise in your organization. Without competent resources such an evaluation cannot be fruitful. One of the ways to develop such competence would be to routinely float questions like ‘why are we doing this task?’ within your maintenance team. Such discussions will help your teams in remaining objective while looking for answers to your problems.
Leave a Reply