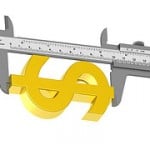
Being able to see what world class Reliability & Maintenance looks like is one thing. Communicating that success and level of performance to non-maintenance people can be difficult. Not to mention, that we always need to improve, and how can we if we only use qualitative measures?
I remember one time, trying to explain how Maintenance Planning & Scheduling has improved our maintenance department. I used explanations like; “The team isn’t wandering around looking for parts” and “They don’t need to leave the job to get the manuals anymore”. I was met with blank stares and was asked “How much were we saving on labour” and “How much were we able to reduce planned downtime”.
We operate in a business and are a service to the operation. We need to be able to express our performance in ways that the other parts of the operation understand. Here are my top 7 Key Performance Indicators in Reliability & Maintenance.
- Training Hours per Person: Is measured on a yearly basis and demonstrates our commitment to growing our staff. It is calculated by totaling up the training hours in a year and dividing by the number of maintenance staff. Our goal is to meet or exceed 80 hours per person per year. This is a key measure in our pillar of Capability & Knowledge Management
- % Planned Work: Is measured weekly and is based on the weekly schedule. The measure ensures that we are focused on Planned Work, which reduces costs. It is calculated by taking the Time Spent on Planned work ÷ Total Maintenance Labour Hours. Our goal is to be >85% and is a key measure in our Work Management pillar.
- Stock Turns: Is measured monthly and is used to ensure that we have the right parts in the storeroom. The equation is Value of Stock Purchased ÷ Value of Stock on Hand. Our goal is to be >2 and it is a measure in our Spare Parts Management Pillar
- Maintenance Cost /Capital Asset Replacement Value: Is best measured yearly and allows the comparison of equipment from different areas. It is calculated by taking the total cost to maintain and repair a piece of equipment over a year ÷ by the cost to replace the equipment with a new one. Our target is <2.5% and is a key measure in our Equipment Strategy Pillar.
- Availability: can be measured weekly, quarterly or yearly and provides a measure of when equipment is running or capable of running. The calculation is MTBF ÷ (MTBF+MTTR). Our goal is to reach >97%. By trending this measure, we are able to see how effective we are at eliminating equipment issues. As such it aligns with our Defect Elimination Pillar.
- Maintenance Cost per Unit Produced: This is best measured yearly and used to demonstrate improvements in reliability and maintenance. It is calculated by taking the total cost of maintenance and dividing by the number or units produced. This is a key measure in our foundation of Business Strategy
- Recordable Injuries: Is best measured yearly and used to demonstrate and drive improvements in safety. If we do not have a safe operation, we should not be worrying about other items. It is calculated by taking the number of injuries ÷ 200,000 working hours. This give us a rate of injuries per 200,000 working hours. Our goal is to be < 0.5. This is an additional measure from our Business Strategy Foundation.
Financial measures such as Maintenance Cost per CARV and Maintenance Cost per Unit can be difficult at times due to the bow wave effect. A small increase in cost as improvements are made, prior to realizing the benefit. In addition, they can be greatly influenced by various changes in the operation or the site, such as increased or decreased production.
All of these measures come from SMRP – Best Practice Metrics. If you are not a member, access to the comprehensive guide is worth the membership fee alone. In addition you can find a great piece of work in the book Maintenance & Reliability Best Practices by Ramesh Gulati.
Remember, to find success, you must first solve the problem, then achieve the implementation of the solution, and finally sustain winning results. What are one or two KPIs that you measure on a constant basis? Have you seen a benefit since you started measuring them?
I’m James Kovacevic
HP RELIABILITY
Solve, Achieve, Sustain
Featured image “Dollar versus Dow” by Bill Brooks
SMRP. (2015). SMRP Best Practices . Atlanta: SMRP.
No Fields Found.
Leave a Reply