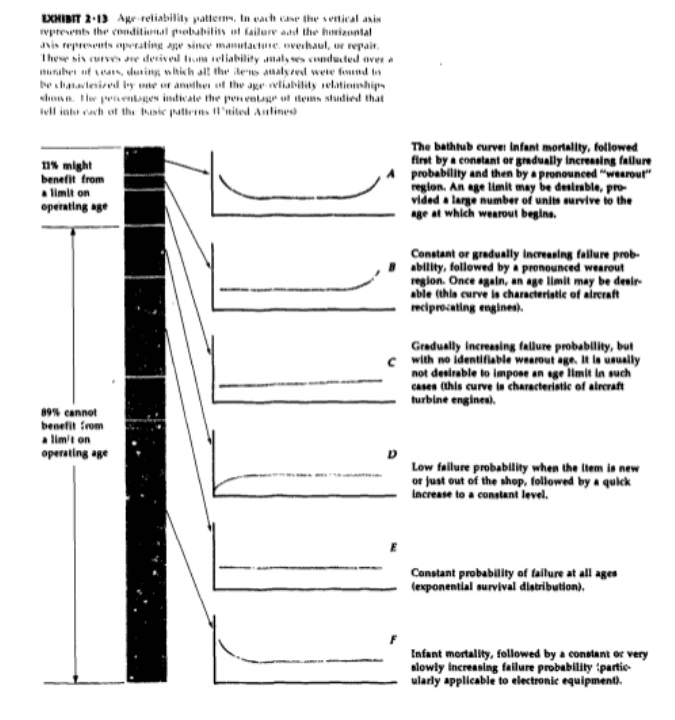
I find the world of maintenance a very odd place to find MTBF. While it is possible, that a set of equipment or a machine may actually have a constant failure rate it is the exception rather than all that common. Assuming a constant failure rate doesn’t make it so.
Recently Ricky Smith posted a link to a copy of the 1978 Nowlan and Heape RCM Study (which is a very good read, btw). One of the elements of the study was the analysis of the failure rate patterns seen by United Airlines. A screen shot of one of the graphics shows six different patterns and they also list the percentage of events that exhibit each behavior.
Only 11% of the items in the study would benefit with preventative maintenance. Note this isn’t the lubrication or adjustment type PM, rather the replacing of parts that are soon to wear out and fail. The remaining 89% have the best strategy of replace upon failure.
I’ve seen this chart or similar charts in other books and presentations. While the numbers are interesting, they really only apply to those items the folks at United Airlines included in the study from the mid ’70s.
If you are running an airline using equipment from the 1970’s and United maintenance program, then you should be doing PM’s on about 11% of your equipment. If not, then you number if items to include will be different and most likely will be different.
Get the data, sort out the failure rate patterns and then make decisions. Simply assuming MTBF and a constant failure rate (or primarily blaming vendors!) is a pretty naive approach. Most organization keep some kind of record on when down time occurs due to equipment failure. Use that data to improve your maintenance program.
The overall RCM document is very good (how we use it sometimes certainly could be improved) and I highly recommend you including this study in your must read list. To make it easy, you can find the complete work here and it is possible to download.
[slideshare id=15833032&doc=nowlanandheapercmstudy-usdodfunded-130102173537-phpapp02&type=d]
Finally, check, recheck and use the data and results to create meaningful information. When I see a study like the RCM study and Exhibit 2.13 I take away there are at least six failure rate patterns and I need to find which of my equipment follows which pattern — then let’s talk about the appropriate preventative maintenance approach.
Your entry and comments, on PM effects on MTBF, were academically interesting and pushed a few of my “hot buttons,” so, here I am responding. I have never been a proponent of predictive maintenance where you go to huge effort to predict MTBF and then replace devices before they break. I push my customers to save their money by rather using effective prognostics, changing the shape of the five MTBF failure curves, which you mentioned, by changing the PoF control factors and by replacing PM with CBM.
Therefore I would rewrite your Tilt for this discussion to: “MTBF and PM” can be transformed to “No MTBF and no PM” by “FISH and CBM”.
Hi Howard,
Thanks for the comment and I wasn’t thinking about PoF and prognostics at all, and you make a good point. In either case understanding how and why equipment fails is much more useful than randomly doing PM especially based on a set of poorly considered MTBF values.
Cheers,
Fred
Frek,
I like to support what u pointed out. MTBF what we can summarize as “If someone put a man half portion in boiling water n half portion in freezing temp then on average he will be comfortable”
Averages cannot give you street level data that results in meaningless finding n hence meaningless solution. What I actully I found at my end when I analyzed the data.
Shifting from MTBF policy needs little bit efforts however it is possible n after devicing some mechanism to capture as much as street level data we can finally come we close to meaningful findings n hence meaningful results
M.Saifuddin,
Maint Program & Reliability Engr
Fred, I would rather say that 89% of the assets/ equipment would benefit from Condition Monitoring (operational checks/tests) or some form if PdM (Predictive Maintenance).
I agree Michael, and neither approach could use MTBF for any reason I can dream up or have heard about.
cheers,
Fred
Identifying and assessing functional, economic, safety or SHEQ consequence of failure opportunity help in prioritizing components or systems in RCM program. The decision tree gives an integrative approach to assign anyone of PM, PdM, CM, CBM, RTF to the system under investigation. Being proactive is also a sort of preventive maintenance. Even for CBM we still need to inspect, test, measure, or capture the value of designated parameters. To do this require knowing how often meaning the need of a MTBF point value.
I think we need to determine the MTBF for planning purpose and even in CBM.
My suggestion is that we still need to estimate the MTBF to use as a starting point and also for reliability growth analysis purpose.
I was with you till you recommended the need for an MTBF to get started…. how about using a useful measure like reliability over a year, or availability over a month, for example. That may serve as a better starting point. cheers, Fred
Thanks for the comment, Thomas. cheers, Fred