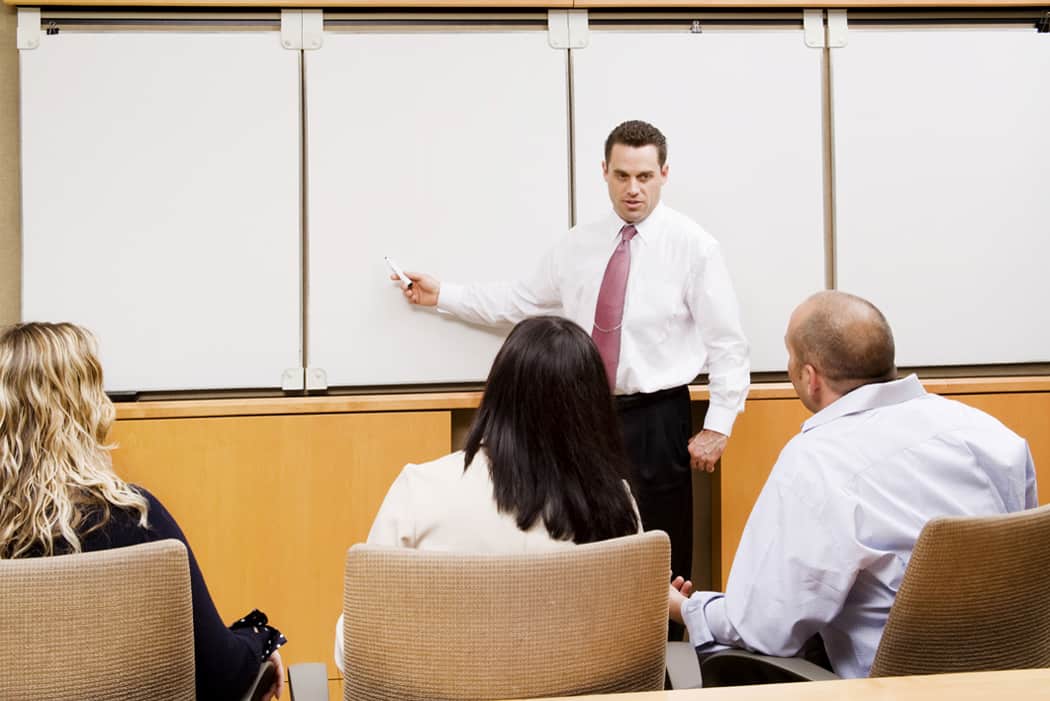
Kirk Gray, Accelerated Reliability Solutions, L.L.C.
In all aspects of engineering we only make improvements and innovation in technology by building on previous knowledge. Yet in the field of reliability engineering (and in particular electronics assemblies and systems), sharing the knowledge about field failures of electronics hardware and the true root causes is extremely limited. Without the ability to share data and teach what we know about the real causes of “un-reliability” in the field, it is more easily understood why the belief in the ability able to model and predict the future of electronics life and MTBF continue to dominate the field of electronics reliability engineering. Please note that I refer to solid state electronics and assemblies. I make a distinction between Failure Prediction Methodologies (FPM) for electronic assemblies (PWBA and systems) that typically has more life than needed (or really known) for most applications, as opposed to mechanical systems (i.e. motors, gears, switches) that can have a more limited life assignable to friction and wear out and have some ability to be modeled.
I have been teaching HALT and HASS methods for over 20 years and a common question I have heard many times is “If HALT is so great, why aren’t there more examples published on its benefits?” There are several reasons why details of real HALT case histories, as well as any other actual empirical electronics reliability data, are rarely published.
Three key reasons are:
- Competitive advantages of not sharing the most effective reliability practices
- Potential legal liability for disclosing real causes of field failures
- Engineers have little time to write and publish.
When a company discovers a new product development process that leads to significantly faster times and lower costs to release a mature product to market, they are not likely to tell their competitors. Doing so would cause them to lose the competitive advantages those new processes. Does your company publish its best methods for product reliability development? So why expect it from any other company?
Legal liability is a huge risk for manufacturers. Failures of electronics systems might lead to significant loss of property or in the worst case human lives. Publishing the cause of electronics failures might provide evidence of liability leading to costly judgments for the product designer or manufacturer. For this reason, most companies will never voluntarily allow failure data to become public. Reliability engineers that may want to help the industry by publishing the real failure data typically face many challenges to have the legal departments give permission to publish. Even if they are able to publish something on actual reliability the paper has so much redacted and “sanitized” for public disclosure that the most significant data may not be published.
It takes time to write and publish any technical paper. In today’s current economic challenges many electronics companies have trimmed engineering departments down to the bone. Engineers are challenged for enough time in the day to complete projects and timelines. Few are motivated to take the extra time necessary, and face the companies’ legal obstacles of publishing the case histories of real field failures of electronics. Without engineers being willing or able to publish the real case histories, details on the root causes of the failures, and best methods to prevent them, little can be expected in the advancement of the science of electronics reliability development and testing.
As previously stated many times in my previous blogs, if the reliability engineers really look at the root causes of field failures in their own products, they would see the same confirming evidence that in general the reliability of an electronics system cannot be predicted from statistics and probabilities. In the 22 years I have spent working with companies to improve reliability of electronics hardware I have seen many root causes of field unreliability in electronics systems.I do not recall ever seeing a wear out mode of a nominal electronic component as a cause field failures. It has always been an overlooked design margin (which may appear to be an early wear out), misapplication of a component, an error in manufacturing, or a misuse or abuse by the user. If I could publish the real evidence and data and root causes of all the failures of electronics in a wide variety of equipment and companies I have worked with, or heard about through colleagues in the field, the case for using empirical stress limit methods of finding weaknesses would be much clearer.
The conditions that limit the sharing of real field reliability data are not likely to change in the foreseeable future. This is why many companies are still doing FPM fundamentally derived from the invalid MIL HNBK 217 methods and still use the meaningless term MTBF. While statistical or probabilistic methods are used for many valid engineering design and analysis applications, they have few applications to predicting the random errors and combinations of events that cause failure solid state electronics. Most electronics systems become technological obsolete before any inherent wear out modes cause failures.
We still can make progress in the field of electronics reliability, but we must validate the methodology and results from engineering basis. We must use our knowledge of physics and material science in electronics, as well as what lessons have been learned in the causes of real field failures. We must make sure when electronics reliability is developed now and in the future that there is traceability and references to the physics of the failure mechanisms. For instance, traditional electronics FPM has used the Arrhenius equation and the broad assumption of 0.7 eV for the activation energy in silicon components as a major factor in predicting the rate of failure of component. This belief continues today, even though there is little or no evidence of traceability to physical mechanisms in today’s components and over 16 years since MIL HNBK 217 was removed as a DoD reference document. .
When we find a weakness in an electronics system through stepped-stress methods, we should know enough about the materials to know whether the weakness is due to a fundamental limit of technology (FLT) such as the melting of plastics, solder, or limits of LCD operation at temperature, or if the weakness is due to the in-circuit application of a particular component. After uncovering the causes, we can understand what physics drove the failure and the element to change to increase the systems strength or capability. Usually it is only necessary to strengthen one or two “weak links”, to bring a products strength up to the FLT. Sometimes those weak links are software, not hardware, and changing code may be the only change necessary to add significant thermal strength capability and margins. Occasionally the system is designed and built and reaches the stress FLT with no change needed, and this becomes a benchmark for subsequent designs. Although, if you are not testing to empirical stress limits, you will never find out.
The causes for the inherent limits in sharing field and test lab reliability data are not likely to change anytime soon. Yet, we can change our orientation and approach to electronics reliability development. Realizing the random and unpredictable nature of most electronics failures in the first 5-7 years of use would result in a major shift in the activities for many companies developing electronics systems. It is a change that has been slowly being adopted by more companies, but they are not going to spread the word to competitors.
The development of reliability based on empirical stress limits still has a long way to go before it becomes the dominant electronics reliability engineering development paradigm and activity. Using the limited data available in your own products failures and physics and material science, must be the basis for validating the use of empirical stress limit methodologies. The need for faster reliability development demands it. I have seen the evidence, but cannot share most of it, that HALT discovery methods are valid regardless of the rapidly changing materials and manufacturing processes in electronics components and systems in the past and know it will be in the future.
“A new scientific truth does not triumph by convincing its opponents and making them see the light, but rather because its opponents eventually die and a new generation grows up that is familiar with it”-Max Planck, Scientific Autobiography
Leave a Reply