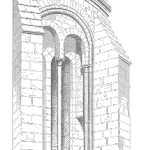
Non-destructive testing of welds. Welding processes and methods can introduce contaminants and metallurgical defects into the weld. If a weld is required to withstand severe loading conditions and stresses it is critical to insure its quality meets minimum standards. Welds can be tested by destructive and non-destructive techniques. Most production is tested by use of non-destructive methods. The most common non-destructive tests to check welds are Visual Inspection, Liquid Penetrant, Magnetic Particle, Eddy Current, Ultrasonic, Acoustic Emission and Radiography. Keywords: NDT, quality control, non-conformance, verification, weld procedure.
When metal is welded the molten puddle cools and solidifies. During cooling the weld quality can be compromised by inclusions such as slag, by human error from fatigue, by wrong set-up and technique, by equipment error due to breakdowns, by environmental effects such as low temperature and moisture, and by metallurgical phenomenon from incompatible metals or high cooling rates. Because welding is highly dependent on factors controlled by humans it maybe necessary to prove the quality of the work is suitably for the duty.
In all the NDT methods described below the certainty of compliance is entirely dependent on the inspector’s ability. High quality results are only possible from trained, competent and experienced people. Do not use unqualified people to do any of the tests you are about to read of.
Visual Inspection
This method uses a qualified and trained observer watching the weld as the welder is working. The observer watches the weld pool and the cooling metal. They typically look for inclusions, undercutting (the weld height is below the parent metal height), depth of weld penetration and certainty of bonding to the parent metal.
When a non-complying defect is observed the spot is marked. At the end of the weld run the defect is ground out and the weld is remade to the required quality.
Liquid or Dye Penetrant Inspection
As the name suggests a colouring agent is used to detect weld defects. This method will only find surface cracks and surface discontinuities. The weld surface is thoroughly cleaned of scale and splatter (but not shot blasted as it will close over the defects). A detergent wash is used to remove dirt, a pickling paste is used to remove paint or grease and a degreaser or solvent is applied to remove oil. Only a clean metal surface is acceptable.
The system normally comes in two spray cans – one is the penetrant and the other is the developer. The penetrant is sprayed over the weld and capillary action draws it into any minute surface cracks. The penetrant on the surface is wiped off and the penetrant in the cracks remains wet. After a short dwell time the developer is sprayed over the weld. The developer acts to draw-out the penetrant dye from the cracks and so changes colour. It behaves like blotting paper and magnifies the presence of the crack.
Magnetic Particle Inspection
This method uses changes in a magnetic field to detect surface and just-below surface discontinuities. When a magnetic field is interrupted by a defect, the field distorts around the defect. Powdered magnetic filings placed in the field can show this distortion. This method is only usable for ferro-magnetic (iron based magnetic) metals.
When used to test welds the magnetic field is produced either by placing metal prods on each side of the weld and introducing a low electric current through the metal or by placing the metal part into a magnetic field. Magnetic fields are induced into the part by the external magnetic field.
Once the magnetic field is established a few powdered, coloured metal particles are placed on the part. The pattern created by the powder in the magnetic field is inspected for field distortions. The particles may be used wet (in a suspension of kerosene) or dry depending on the parts location and the purpose of the examination.
Eddy Current Inspection
The principle of operation is the detection of changed electric current flow in a coil of electric wire. Alternating electric current flow through a coil creates a fluctuating magnetic field around the coil. If the magnetic field is brought close to conducting metal, eddy electrical currents develop in the metal. The eddy currents in turn set up a magnetic field in opposition to the coil’s primary field.
Any fluctuations in the secondary magnetic field due to distortions also change the strength of the primary field, which in turn change the electrical current flow through the primary coil. The change in primary coil current flow is detected. The amount of the current change represents the effect of a discontinuity causing the distortion in the secondary field.
This method is used to detect weld defects deep into the metal. Depths of up to 25 mm are possible depending on the metal being tested and the speed of at which the alternating current changes (its frequency).
This is the favoured approach for testing steel tank floors and walls. A crawling scanner is sent across the surface and changes in the eddy current are shown on a monitoring screen. Where evidence of a discontinuity is found the spot is marked and then a more thorough local examination is conducted with other NDT equipment to quantify the defect.
Ultrasonic Inspection
High frequency sound waves are sent into a metal using an emitting probe. If the waves encounter a discontinuity they bounce off it and return to the probe where they are detected. The size and location of the discontinuity are displayed on a monitoring screen.
The method cannot be used for surface and near surface faults. A dead-zone occurs just below the contact point of the probe. To insure proper acoustic connection between the probe and metal surface a liquid coupling agent, like grease, is used between the two. The test surface is required to be smooth enough for the coupling agent to maintain contact between probe and metal. Where the weld is peaked too high a different technique is required that uses reflected sound to check for discontinuities.
The sizes of defects that can be detected depend on the wavelength of the sound. As a rule the defect has to be half the wavelength to be detectable. Different metals have different wavelengths for the same sound frequency. In steel at 2 MHz, defects of 1.5 mm are detectable.
Acoustic Emission Monitoring
Acoustic emissions are stress waves produced by sudden movement in stressed materials. When a material is placed under load it deforms ever so slightly. Internal movements produced by the deformation create sounds that travel through the structure. These sounds can be detected and the source of the movement located. Once the source is found other NDT techniques are used to quantify the movement and any presence of discontinuities.
This method is often used on existing large structures, such as tanks and pressure vessels, as it is fast and low cost. Fixed sensors are located on the structure and typically placed every 1 to 6 meters apart. The structure is ‘loaded’ in rising, step-wise fashion and the acoustic emissions recorded on a display monitor. The loading is varied or held constant for a period of time and the changes in acoustic emissions indicate if the structure is continuing to move internally.
By factoring-in the metal’s sound velocity, the emission point can be located by triangulation with good accuracy. Background noise can interfere with results. This problem can be overcome by stopping the noise at its source, by filtering it out using the electronics within the monitoring equipment or by use a different measuring frequency to the noise frequency.
Industrial Radiography
Radiographic inspection is based on the absorption of radiation by materials of different density. In the engineering industry X-rays or gamma rays are used. It is an expensive process but penetrates almost all materials to great depths.
The radiation source is put on one side of the weld being tested and the detecting ‘photographic’ film is placed on the other side of the weld. As radiation passes through the weld discontinuities act as density reducers allowing more radiation through them. The high level of radiation shows up as a darker colour on the film.
Because the image created on the film is a ‘shadow’ it can be affected by factors such as changes in subject thickness, radiation scatter, geometric factors influencing radiation, source positioning, exposure times and film quality.
Mike Sondalini – Equipment Longevity Engineer
References: Getting the most out of NDT, Dr G. G. Martin, Attar, (www.attar.com.au)
We (Accendo Reliability) published this article with the kind permission of Feed Forward Publishing, a subsidiary of BIN95.com
Web: trade-school.education
E-mail: info@trade-school.education
If you found this interesting you may like the ebook Bulk Materials Handling Introduction.
Leave a Reply