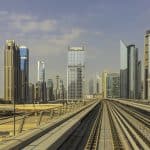
Understanding the Business Benefits of an Asset Management Program
Have you tried to upgrade / replace a piece of equipment due to the high cost of maintenance? What about having the process stopped by procurement because they are not aligned with the high upfront cost?
While there is a generally a common goal of ensuring the long-term success of an organization, the approach is not always cohesive. An asset management program is there to ensure an integrated and cohesive approach is in place. This cohesive approach ensures the organization is working towards a common goal. [Read more…]