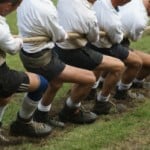
Tie all the Roles & Responsibilities Together in an Easy To Use Document
This is the final post in the series on roles & responsibilities and is the final step in ensuring the team is working together. So far in the series we cover the importance of defining role & responsibilities. How to determine roles & responsibilities, and the major roles in the maintenance department. In the last post, we will cover how to tie it all together in a simple, easy to use document. A RACI. [Read more…]