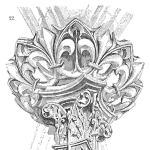
The concept of degradation variables
Assets typically age over time, leading to degraded performance and loss of function. Asset life models are built in order to predict future degradation patterns. Those models are based on asset degradation variables such as time or usage. Those variables could be for example, time between failures or distance covered between failures. Many assets have more than one degradation variable. In this case, it is important to define which of the multiple variables is the dominant one and will subsequently provide the Reliability Engineer with the most precise life model.
Reliability is a probability. Specifically, the probability that a system will perform its intended function within a specified mission time and under specific process conditions. Therefore, most reliability calculations incorporate a time element as a degradation variable. Generally, when building life models, we default to using calendar time as it is more straightforward. We have had tools to easily measure elapsed calendar time for centuries now. [Read more…]