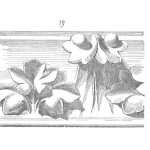
I had to learn a lot to become a transformer reliability leader. I have an engineering background and a transformer maintenance and testing background, but to be the practitioner I wanted to be I had to get educated. I sought out reliability knowledge. I found much of that knowledge through reading and research. It started with Google searches and Wikipedia articles, and it eventually led to half-a-dozen subscriptions to magazines and journals related to the field. It’s incredibly important to keep up-to-date with the industry and with reliability. [Read more…]