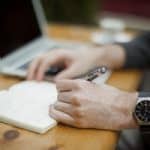
Why Failing Can Be Good and What You Can Take Away from It.
Regardless of how good a maintenance & reliability program is set up and managed, there will be failures. This is partly due to the maintenance program itself, where the focus is on the consequences of the failures, not the failures itself. This approach allows most organizations to manage large facilities will a minimum of staff and cost.
But what should happen when something does fail? Should we just carry on as usual since we avoided the consequences? Absolutely not. When a failure occurs, we need to learn from it and improve the maintenance & reliability program. Yet, many organizations address failures by implementing a PM routine. This is not the right approach. Remember only 11% of failures are age-related. Adding these PM routines to the program will cause a collapse of the program from too much work, not to mention the maintenance induced failures that result from it.
So what should happen? The failure should be analyzed and actions implemented to reduce the chance of the failure occurring again.
[Read more…]