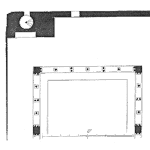
Written instructions make it clear.
Written directions given to maintenance tradesmen to reduce the chance of making an error and to reduce time spent looking for information are called job procedures or job instructions. [Read more…]
Your Reliability Engineering Professional Development Site
A listing in reverse chronological order of these article series:
by Mike Sondalini Leave a Comment
Written instructions make it clear.
Written directions given to maintenance tradesmen to reduce the chance of making an error and to reduce time spent looking for information are called job procedures or job instructions. [Read more…]
by Doug Plucknette Leave a Comment
The following article came about from an on-line conversation I had with a follower who responded to an article I had written on the differences between Leaders and Managers. Her hope was that someday soon someone in a leadership position at her company would recognize the harm her boss was causing and how miserable he had made the lives of those who worked for him.
So as promised here is my take on working for a bully boss!
If you’re lucky you only work for one in your lifetime. [Read more…]
Imagine an operation in which there are no lost time accidents, OEE is increasing and there is a plan to address the skills shortage. These sites do exist and chances are they using procedure based maintenance. Procedure Based Maintenance is simply having all maintenance activities documented in a procedure. These procedures are then followed step by step when conducting breakdown, corrective and preventative maintenance. [Read more…]
by Mike Sondalini Leave a Comment
What readers will learn in this article.
Couplings are used between shafts to connect them so power can be transmitted and to allow for axial expansion. Shafts can either be aligned or intentionally inclined at an angle to each other. When at an angle a universal joint is used to connect the shafts. When aligned a shaft coupling is fitted. [Read more…]
by Doug Plucknette Leave a Comment
When people first begin to learn about Reliability Centered Maintenance and methodologies like RCM Blitz, they get excited about the potential results that can come from performing a RCM analysis and implementing the resulting tasks. Shortly after completing their RCM Training some begin to understand that good RCM takes leadership, structure and discipline, others begin to think of ways to shortcut the process. [Read more…]
by James Kovacevic Leave a Comment
Understanding the how equipment failures along with utilizing a proven and effective approach to developing an equipment strategy is a winning combination for manufacturers everywhere. When combing the knowledge and the system, manufacturers can yield significant improvements in their operation, such as a reduction in PM workload of 22% with gain 4% in line efficiencies. Or how about a reduction of 42% of PMs, without a single loss in equipment availability. It is possible and required for manufacturers to become and remain profitable. [Read more…]
by Mike Sondalini Leave a Comment
Shaft alignment on pumps. Shaft misalignment is one of the most common reasons for bearing and mechanical seal failures. Rotating misaligned shafts produce vibration and complex fluctuating radial and axial loads that lead to breakdowns. Shaft alignment is a precision maintenance requirement that requires exacting care and detail and if not performed will cause much production down time.
Keywords: axial alignment, laser alignment, dial indicator, soft foot, shaft coupling. [Read more…]
I want my customers to be successful, every one of them. Yet there are times I can see the writing on the wall and I know as hard as I might try to show them a clear path to what it takes to be successful they have their own plan. Some of them are so complex that people become confused just trying to make sense of them, and others get so hung up in the minutiae of even the simplest of steps like listing a 3 part failure mode they will word-smith themselves to a point where folks just give up. I find myself asking “why do people have to make what is really so simple into something that appears to be complex?” [Read more…]
by James Kovacevic Leave a Comment
Knowing How Equipment Fails Allows Effective Plans to Be Put In Place and Improve Equipment Reliability
In the 1960s the failure rate of jet aircraft was high even with the extensive maintenance programs that were put in place to prevent the failures. The programs required overhauls, rebuilds and detailed inspections which required the various components to be disassembled. All of these activities were based on an estimated save life of the equipment. [Read more…]
by James Reyes-Picknell Leave a Comment
Being proactive with your assets is all about managing failures before they occur. You can reduce or eliminate the consequences of failure by forecasting what is likely to happen and deciding in advance about what to do about it. The advantage to doing this is that major business impact due to equipment breakdown can be avoided. High performing companies manage proactively – they foresee and avoid problems. It’s good for business! [Read more…]
Fibreglass construction and repair. Fibreglass is a glass fibre reinforced plastic composite with excellent chemical resistance properties. Its physical properties, selection of resins and glass, method of construction and fabrication and peculiar repair requirements must be appreciated when using this material.
Keywords: laminate, backing layer, structural layer, corrosion barrier, crack repair, winding angle. [Read more…]
by Doug Plucknette Leave a Comment
Something light to read on a Monday afternoon.
I’m beginning think that one of the worst side effects of growing older has nothing to do with the fact that you are not as active as you should be, but that you spend that time where you should have been walking, running, riding a bike or chasing the kids thinking about crap that might have little significance to the rest of the world. [Read more…]
by James Kovacevic Leave a Comment
Making the criticality analysis work for you and drive improvements in the maintenance strategy
Most manufacturers do not have an up to date criticality analysis and those that do have one, do not use it to drive decisions. Having a criticality analysis facilitates improved decision making and prioritization within the site and business.
How many times are there debates regarding which work needs to be done, which PMs will be dropped from the schedule because the planned downtime was reduced? These debates occur regularly, but to not have to occur. A criticality analysis drives improvements in the business by: [Read more…]
by James Reyes-Picknell Leave a Comment
Your upfront capital investment must go beyond engineering, procurement and building costs. Additional activities that will need to be done that fit within the 2 – 3 % of capital cost figure are:
RCM analysis on the new design (preferably at both concept and detailed design phases so you can incorporate design change recommendations easily) [Read more…]
by Mike Sondalini Leave a Comment
What readers will learn in this article.