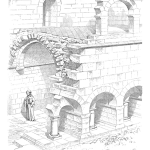
Many people believe Proactive Maintenance is the ultimate physical asset management strategy—but there is one better strategy. To get world class reliability at the least cost there must be no maintenance. Only a “wellness” paradigm can achieve that result.
[Read more…]