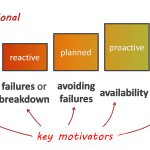
In the late 1970s, Hewlett Packard was a company that valued quality compliance, certification and awards. But the then Chief Executive Officer noticed a problem. He (on a hunch) initiated an analysis of ‘quality related expenses.’ He wanted to quantify the cost of defects and failure. The results were terrifying. [Read more…]