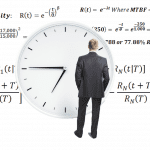
One of the most difficult challenges of incorporating reliability activities with program planning is estimating the time it will take to demonstrate reliability. Demonstrated product reliability is typically measured as a confidence in a product’s capability to achieve a reliability goal. At product release, the business unit may feel comfortable with their target market and warranty goals with a demonstration of a 90% confidence in the products reliability goal of 99.1%. [Read more…]