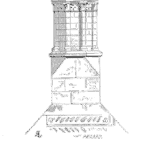
Most reliability engineers are familiar with the life cycle bathtub curve, the shape of the hazard rate or risks of failure of a electronic product over time. A typical electronic’s life cycle bathtub curve is shown in figure 1. [Read more…]
Your Reliability Engineering Professional Development Site
A listing in reverse chronological order of articles by:
Most reliability engineers are familiar with the life cycle bathtub curve, the shape of the hazard rate or risks of failure of a electronic product over time. A typical electronic’s life cycle bathtub curve is shown in figure 1. [Read more…]
by Fred Schenkelberg 4 Comments
Fault Tree Analysis (FTA) is a technique to explore the many potential or actual causes of product or system failure.
Best applied when there are many possible ways something may fail. For example, when my car doesn’t start, it could be a dead battery, faulty started, loose wire, no fuel, and on and on. [Read more…]
by Fred Schenkelberg 9 Comments
Customers experience product failures.
Understanding these failures that occur in the hands of customers is an essential undertaking. We need this information to identify increasing failure rates, component batch or assembly errors, or design mistakes. [Read more…]
Historically Reliability Engineering of Electronics has been dominated by the belief that 1) The life or percentage of complex hardware failures that occurs over time can be estimated, predicted, or modeled and 2) Reliability of electronic systems can be calculated or estimated through statistical and probabilistic methods to improve hardware reliability. The amazing thing about this is that during the many decades that reliabilityengineers have been taught this and believe that this is true, there is little if any empirical field data from the vast majority of verified failures that shows any correlation with calculated predictions of failure rates.
[Read more…]
by Fred Schenkelberg Leave a Comment
Estimating the set of stress and stress curves is an interesting exercise that may have a greater purpose: safety.
The connection is clear when considering the potential consequences of failure.
For example, the loss of braking power when landing an aircraft may result in the aircraft rolling off the end of the runway. This could be into a river or road and may have a rather poor outcome not only for the aircraft. [Read more…]
by Fred Schenkelberg 3 Comments
Ideally, in every design of every component, the stress–strength relationship looks like this figure. The stress is well below the strength.
This implies there is very little chance of failure due to the element being overstressed.
Also, ideally, we fully characterize all stresses and all strengths for each element of a product. This is generally difficult to accomplish and it is rarely done to that extent.
by Fred Schenkelberg Leave a Comment
Every once in a while I see a comment that by following the HALT methodology you will “over design” a product.
Many question at what point or operational limit do you quit increasing the stress-strength margins. Those who hold this view of HALT do not understand the essence of what was Gregg Hobbs’ principles and paradigm shift. [Read more…]
by Fred Schenkelberg Leave a Comment
Reliability or life testing involves estimating the expected durability over time of an item.
This may be an entire system, a product, or an individual component. We may also focus on an element of a component, such has a material property.
At the end of the testing, we want to say something meaningful about the expected performance over time. [Read more…]
by Fred Schenkelberg 2 Comments
Highly Accelerated Life Testing (HALT) is a technique to expose weaknesses or faults with a product.
HALT uses individual or combined stresses in a step stress approach to quickly apply sufficient stress to reveal defects.
HALT is not a specific chamber or fixed set of test conditions. It is an exploratory process to reveal weaknesses in a design.
The product development process naturally includes a check step, to determine if the expected functions of the product work as expected.
Some teams then add a measured amount of stress (temperature, vibration, dust, load, etc.) to the product to explore functionality at elevated stress levels. [Read more…]
by Fred Schenkelberg 1 Comment
In short, you probably do, better reliability performance the better the brand image.
When I’m making a purchase I prefer to buy items that I either have personal experience work well over time (reliable) or have many comments and reviews noting the durability.
As a reliability engineer, I am often asked what kind of car I drive (a Toyota Highlander, if must know). Reliability does matter -not only to me- it matters for many making a buying decision.
When a product’s actual reliability performance exceeds the customers expected reliability performance, the customer may consider the product reliable. This experience builds and when supported by other experiences from the same brand, increases brand equity. High brand equity permits a price premium, increased brand loyalty, and increased positive word of mouth support. [Read more…]
by Fred Schenkelberg 2 Comments
Why do so many avoid failure?
In product development of plant asset management, we are surrounded by people that steadfastly do not want to know about or talk about failures.
Failure does happen. Let’s not ignore this simple fact. [Read more…]
by Fred Schenkelberg Leave a Comment
Everything varies.
Your vendors provide components with a range of values. Your production process varies, too.
Creating, monitoring, and maintaining process stability enhances your product reliability performance.
When I started my professional life as a manufacturing engineer, a senior engineer told me we take a product design and can only make it worse.
He said if we could make every unit exactly according to the nominal values of the drawing, every unit would work well. [Read more…]
by Fred Schenkelberg Leave a Comment
The trite answer is just as many samples as you need and not one more.
A better answer is enough samples to make the right decision. The realistic answer is you will not enough samples.
“How many samples?” is an oft-asked question when planning for quality or reliability testing. [Read more…]
by Fred Schenkelberg Leave a Comment
A break from the normal format.
Reliability.fm is a podcast network focused on reliability engineering topics.
Starting with three shows. Speaking of Reliability and Dare to Know described below, along with recorded Accendo Reliability webinars. [Read more…]
by Fred Schenkelberg 2 Comments
Failures happen. Sometimes product failures happen quickly.
You just bought a new feature rich computer and discover it doesn’t work. Right out of the box, it will not power up. Conversations with the tech support and it’s a trip back to the store.
The failures that occur early the in the life of a product tend —
this ‘tend’ really is just a vague ‘in general’
…tend to occur because of manufacturing errors or shipping/installation damage.
Not always, though. [Read more…]