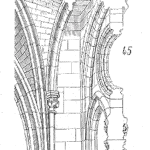
Worst-case tolerance analysis is the starting point when creating a tolerance specification.
It is a conservative approach as it only considers the maximum or minimum values of part variation—whichever leads to the worst situation. Setting tolerances such that the system will function given the expected variation of manufactured components improves that ability of the system to perform reliably.
In the worst-case method, you simply add the dimensions using the extreme values for those dimensions. Thus, if a part is specified at 25 ± 0.1 mm, then use either 25.1 or 24.9 mm, whichever leads to the most unfavorable situation.
The actual range of variation should be the measured values from a stable process. It may be based on vendor claims for process variation, industry standards, or engineering judgment. [Read more…]