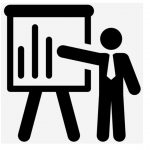
In last month’s article we discussed the most common FMEA mistakes and how to convert them into quality objectives. This month we will focus on how to audit FMEAs, using the FMEA quality objectives as a guideline.
“Twice and thrice over, as they say, good is it to repeat and review what is good.” Plato