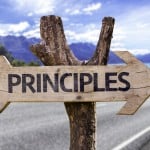
Stand Like a Rock
Nothing can undermine FMEA results more than approaching the subject from the wrong philosophy. In this article readers will learn how use key focus areas to achieve effective FMEAs in all applications.
“In matters of style, swim with the current; in matters of principle, stand like a rock.”
Thomas Jefferson
Definition of “philosophy”
According to the Oxford English dictionary, “philosophy” is defined as “a theory or attitude that guides one’s behavior.”
What is philosophy, and what does it have to do with FMEA?
FMEA is a tool that exists in the larger framework of quality and reliability processes. If one’s approach to achieving quality and reliability is sound, then it will properly guide the use of the FMEA tool. Basing one’s approach to FMEAs on wrong principles, such as fixing existing problems rather than anticipating and preventing them, or on incorrect objectives, such as “to fill out a form” or “to comply with a mandate,” will reap unsatisfactory results.
Underlying philosophy of FMEAs
Through the synergy engendered by the right team of experts, and by implementing correct and proven methods and procedures, problems can be anticipated and prevented resulting in safe and trouble-free products and processes, with the inherent risk in any system or process reduced to a very low level.
Key focus areas for effective FMEAs
The following is a listing of key focus areas for effective FMEAs. It is not meant to be an exhaustive list, but rather the focus areas that the author feels are important to successful FMEA application. Each of these focus areas provides important input to successful FMEA application.
Having the Right Objectives
– Focus on problem prevention
– Focus on design and process improvements
– Leverage FMEAs to improve test plans and process controls
– Select FMEA projects based on preliminary risk assessment
– Keep it simple
Having the Right Resources
– FMEA is a team-based activity
– Fully understand the basics of FMEAs
– Provide skilled FMEA facilitation and unleash FMEA team creativity
– Benefit from real-world lessons learned
– Management plays a key role in establishing and supporting an effective FMEA process
– Support the natural passion and energy of employees to achieve trouble-free products
– Utilize the wealth of knowledge in the fields of quality and reliability
Having the Right Procedures
– “Make it visible”
– Ensure FMEAs are requirements-driven and data-driven
– Ensure FMEAs always get to root cause and actual failure mechanisms for high-risk issues
– Keep the focus on areas of concern and risk
– Perform FMEAs within the right time frame
– Fully execute all actions to ensure risk reduction to an acceptable level
Examples of using correct philosophy to guide FMEAs
From the above list, three example excerpts follow, from the book Effective FMEAs.
Focus on problem prevention
Preventing problems saves money and improves products. Fixing problems is necessary when they occur, but is substantially more expensive than problem prevention. There is a different mindset in an organization that focuses on problem prevention; and the tools and timing are different. FMEA is a key tool to prevent problems before designs reach testing or processes reach the plant floor, and to improve tests and controls to be sure problems do not reach consumers. The emphasis for FMEA should be problem prevention.
Focus on design and process improvements
In order to achieve safe and reliable product and process designs in a timely manner, it is essential for FMEAs to drive design and process improvements as the primary objective. Safe and trouble-free designs and stable, capable and error-proofed manufacturing processes must be the primary goal. FMEAs need to drive action strategies that improve designs and processes.
FMEA is a team-based activity
To be successful, FMEAs need the right team of subject matter experts. Even the best engineers have blind spots and only a team composed of the right disciplines can provide the necessary input and discussion to ensure all concerns are surfaced and addressed. FMEAs should not be performed by one or two individuals, or with the wrong team composition.
Application Tips:
1. It is easy to get caught up in filling out the FMEA form. It takes practice and effort to keep the FMEA team guided by proper philosophy. It is helpful to remind the team of the focus areas of FMEA, such as prevention, design improvements, and test improvements.
2. One example of proper application of prevention is to treat anticipated problems discovered by the FMEA team with the same priority as actual problems that have occurred in the field. Management can support a culture of prevention by including FMEA anticipated high-risk issues in the same meetings that they address field problems.
Next week
In the next article, we’ll present problems (and solutions) about FMEA philosophy and focus areas that will challenge both beginners and people who’ve “been around the block.” Stay tuned.
Leave a Reply